International IIoT Perspectives: Precision Agriculture
In the United States, precision agriculture is one of the largest industries by both operational scale and economic impact. The technology utilized is typically on the cutting edge, especially for automation and control. Things like sensors, programmable radios and generally more complex software applications have allowed that industry to evolve, domestically, to a point where land and other resources are used optimally. Internationally, although there have been ‘smart’ or ‘precision’ practices in certain sectors of agriculture, many countries are just now starting to adopt the technology to its fullest extent, including the ability to innovate via start-ups and new practices. India & the Digital Agriculture Revolution According to an article in India Times (image credit), the country is aiming to secure a 20 percent stake in the IoT market share in the next five years through its ‘Digital India’ initiative. While many might look at India and think of the sprawling and diverse urban environments that could offer some potential complications for IoT, it is rural areas seeing the most interesting developments. There has been a noticeable growth in tele-medicine operations, which can allow patients in remote areas to interact with doctors for consultation, eliminating the need to get to a city, or vice versa. Perhaps an even greater area of growth lies in the agricultural realm. According to the article, agriculture employs 50 percent of the country’s population, so the potential for a digital revolution is high. Farmers are just starting to implement sensor technology, automation hardware, and even leading-edge tools like voluntary milking systems the allow cows to be milked on an automated machine according to biological needs. Israel’s Precision Ag Start-Up Community In Israel, where IoT technology is starting to mature, the name of the game is data collection and analytics. Mobile applications, sensor data collection hardware, and advanced analytics software are three areas that Israel is seeing significant market growth, according to Israel21c: Israel stands out in precision-ag subsectors of water management, data science, drones and sensors, says Stephane Itzigsohn, investment associate at OurCrowd. … “Multiple startups are aiming toward the same goal — providing good agricultural data — but approaching it from slightly different angles,” Itzigsohn tells ISRAEL21c. “One might use satellite images or aerial photography; another might use autonomous tractors. Not all will get to that peak in the long journey of farming becoming more efficient.” For example, CropX, an investor-backed advanced adaptive irrigation software solution, can be placed throughout a farming area and synced with a smart phone, allowing the operators to receive real-time data updates on things like soil and weather conditions. CropX is based in both Tel Aviv and San Francisco, indicating that the technology may be poised for wide international adoption in the future. Analytics Drive Italy’s Drought Recovery Italy is perhaps best known for a single agricultural export: wine. However, many would be surprised to find out that it is one of the top corn producers in the European Union, producing more than 7 million tons of corn in 2015, according to an RCR Wireless report. In 2016, the EU’s total corn output dropped noticeably due to year-long droughts affecting production. In Italy, start-up companies collaborated with industrial ag operations develop and deploy widespread soil sensor and water automation technology to help streamline farming practices and create a more efficient system for resource use. The technology allowed farmers to get a comprehensive look at their operations and identify high and low yield areas in order to better utilize the available space. Precision Agriculture and the Industrial IoT The continued maturation of IIoT technology is enabling countries around the globe to better utilize resources like water, energy, and land area to create better agricultural operations. As populations continue to expand, and food production becomes even more important, being able to connect these technologies across the globe could become a key factor in optimizing crop output in critical areas. Imagine the above farm in Italy being able to send its data to data scientists in Germany or the Eastern Europe who could in turn analyze it and provide actionable feedback. Or an industrial farm in Israel managing its yields sending that information in real-time around the country. These possibilities are not far off, and as the networks, hardware and software continue to be adapted, the future of precision ag internationally, will become the present.
5 Reasons Why Your IIoT Network Needs Wireless Programmability
If your company is grappling with the shift towards wireless connectivity and automation, you’re certainly not alone. As more processes are automated, especially within industrial markets like oil and gas or utilities, data has become a valuable asset that provides critical information for operations and performance. Up and coming industry leaders are pushing for modern Industrial IoT (IIoT) networks, as the older, more traditional workforce heads towards retirement. As a result, the processes of yesterday are being phased out – especially when it comes to choosing between hardwire and wireless for remote deployments. For many, wireless solutions have been accepted for some time as the primary means in which data is collected, transported and analyzed. Frequency Hopping Spread Spectrum (FHSS)-based technology in particular is proven to be a reliable and maintainable wireless option. Now, however, we are facing an entirely new realm of opportunity with FHSS-based programmable wireless technology that is molding the future of data collection. Here are five reasons why you need to consider programmable wireless technology for your IIoT network: Bring it all to the Cloud – Programmable wireless solutions are equipped with the ability to incorporate custom, third party applications at the Edge. When we talk about the Edge, we essentially mean the outermost layer of the network. For industrial networks, the Edge is often a remote area where mission critical operations occur. In order for the business to capture a holistic view of their entire network, many have added sensors and other data-capturing devices at the Edge. By adding third party applications with new programmable wireless technology, businesses are able to expand automation capabilities, reduces costs, simplify operations and enable data transmission directly to a private or public cloud. Smart Data Over Big Data – The goal of achieving ‘Big Data’ is common practice in most modern IoT and IIoT networks. Decision makers recognize the power of data and know they need to receive it from every network end-point. We’ve seen this to be true purely in the proliferation of sensors and IoT devices deployed across the U.S. that continues to grow. Having programmability at the edge of the network offers a big advantage, because you have the ability to control of the quality of the data. Even better than Big Data is access to the specific, timely data that is most pertinent to your business operations. Robust and Reliable Technology: Programmable wireless solutions are equipped to embrace the future of data collection. The beautiful thing about these solutions is that the backbone of the technology is FHSS. This particular Radio Frequency (RF) technology has been proven in some of the most adverse conditions imaginable. These technologies are trusted by the government to maintain their links and have proven to operate in some of the most dreadful and intense environments in the world . Where performance is critical – these solutions have proven to work for decades and now programmable options can reliably bring this data directly to the cloud. Flexible and customizable– We are all privy to the fact that no two networks are the same. With programmable options, radio functionality is customizable to the specific needs of the network. Despite the variances, remote networks likely have one thing in common – data needs to be transported across significant distances. Programmable wireless technology is built to be deployed at nearly any point in the network where sensors are collecting data. This is an area in which traditional hardwire solutions almost always fall short, as most businesses cannot afford the cost of running hardwire to these remotes sites. Besides, there are wireless options that are built for easy installation and long-range communications that simply make the most sense for remote deployments. Meeting Modern Demands– Today, IT and OT departments are one in the same. These modern networks eliminate barriers which is conceptually great for operations. However, like any major disruption, convergence has created a number of challenges from visibility, to cultural difference, to security. To ease some of these tensions, modern wireless solutions are designed to drive connectivity for the entire network, and are even able to tie in legacy systems from the field. Many FHSS-based technologies offer secure-data transmission, and by leveraging the programmable wireless technology, and you can bring data to the cloud. Wireless technology is recognized as a necessary solution for remote operations. As IIoT networks mature, there are stark advantages in leveraging programmable solutions. Not only do they rack up cost savings and streamline operations, but they are deployed at the edge of the network with minimal hassle and are built to deliver in any environment.
Remote Tank Level Monitoring and Automation
Industrial livestock operations have several critical needs in order to function smoothly, but perhaps most important is also the most fundamental: water. On remote sites, tank level monitoring and automation are tools that can essentially make or break the entire operation. In many of these situations, the needs of the site managers are different, so in order to maximize the technology being deployed to drive the automation process, they need to be able to customize the functionality. For operations using radio communication networks, those radios need to provide maximum programmability in order to host third party applications specific to the needs of the site managers. We recently finished a deployment that serves as an excellent case study for remote site tank monitoring deployments and included some interesting uses of radio programmability: The operator of a Rocky Mountain based livestock facility approached FreeWave to assist in remote data visualization of water tanks that are vital to its operations. The pain point was that the tank levels could only be observed visually on premise. After consideration of the terrain (mountainous, remote and big temperature swings), sensors and communications infrastructure, FreeWave engineers recommended ZumLink IPR with the Node-RED programming language for intelligent tank data visualization via browser or mobile device. The facility has minimal to zero staff most of the time. If a fault occurs such as a leak that prevents a tank from filling, the facility operators are unaware until they visually inspect the remote faulty tank, located a half mile from property headquarters. The operators wanted to reduce the number of trips to the tank facility and remotely monitor all tanks via web-based browser or mobile device. For the complete case study, visit this link: https://www.freewave.com/case-studies/remote-tank-monitoring-automation/.
Microgrids Gaining Mainstream Traction
While “going off the grid” is not a new term, microgrids are finding new footholds in a changing utilities industry. Recently, more and more cities and states are turning to microgrids not only as highly effective ways of increasing energy resiliency, but also as pragmatic and cost effective strategies for shifting population densities and energy consumption behaviors. Below, we’ve gather some of the top recent headlines on the changing microgrid landscape. Microgrids In New Applications Microgrids have long been viewed as an excellent tactic for supplying power to rural areas and island communities. However, recent data shows that microgrids may be expanding. This article from the Motley Fool, notes that governments and correctional facilities are turning to micrograms as viable options for emergency backup power. Another area where microgrids are seeing growth is in use for growing suburbs and rural areas. In the past, power companies has to build costly new transmission lines to service growing population areas, lines which may only be used during peak demand for a few hours a year. By leveraging microgrids, energy companies can build cost effective solutions for dealing with rare power consumption spikes. Communities Turn to Microgrids for Energy A recent article from Electric Light & Power notes that there are developing plans to build 13 microgrids across the state of New Jersey to increase the areas energy resiliency and better prepare the state for emergency situations. The effort, spearheaded by New Jersey Board of Public Utilities President Richard S. Mroz, has been prioritized in the wake of the devastation caused by Hurricane Sandy, during which many areas were left without electricity and running water for weeks on end. One of the proposed microgrids in downtown Trenton would connect several important government buildings, helping keep the cities most essential resources up and running even during emergency situations. Building a Carbon Free City In the stretch of land between the city of Denver and its airport, a new town is being built that will rely solely on a microgrid for power — and it will be completely carbon free. The city, called Peña Station Next, will rely primarily on solar energy and is receiving large financial support from the city of Denver. As reported in this article from The Scientific American, the city will rely “mainly on solar energy, a king-sized lithium-ion battery and various energy efficiency schemes” for its power. Will Battery Tech Change Microgrid Strategies? Batteries are getting bigger — so what does that mean for microgrids? As noted in this article from Teslarati.com, Neoen and Tesla recently announced the creation of a 100MW/129MWh battery adjacent to the Hornsdale wind-farm in South Australia. One of the claims Tesla had in building the battery is that the company could make money by providing off-the-grid backup power. According to the article, however, this might not be so simple. Bruce Miller, a principal consultant for Advisian, says the 80-minute discharge time for Tesla’s system isn’t in line with 10-megawatt- and 20-megawatt-hour systems that could produce $2.1 million a year from supplying backup energy. Brooklyn is On-Board with Microgrids Brooklyn, the dense suburb of New York City, is one of a growing list of major population centers to explore microgrids. As noted in this article from Green Biz, Brooklyn is exploring a strategy where a virtual web of buildings whose owners can buy and sell power to each other using blockchain technology to manage the transactions. Currently, the program has hundreds of participants signed up, and users will ultimately be able to control their participation through the use of an app. With more governments and power companies exploring the promise of microgrids, it may only be a matter of time before a microgrid is a viable primary or emergency energy option for many. Where do you see microgrids growing next?
Do Drones Help or Hurt Wildfire Fighting?
Summer wildfire season is in full swing across North America, and the question of the utility of drones is once again in the headlines. The technology has proponents on both sides, but it has also been linked to several incidents, including the grounding of critical aircraft in a firefighting effort in Arizona. A key point of differentiation in this discussion is the use of personal drones, similar to the one mentioned in the article above, and commercial drones designed to serve a specific purpose in operations, similar to military or first responder deployments. The problem that firefighters face is the unauthorized use of personal drones, which can create dangerous situations for support aircraft like helicopters and tanker planes. Because firefighting aircraft fly at such low altitudes, they share the same airspace as commercial or personal drones, and at that altitude, one instance of interference can be deadly. A recent Quartz article pointed out the correlation between drone interference and the effect it can have on the people most impacted: civilians and the firefighters themselves: The drone problem has plagued fire departments for the last few years; In 2016, during Utah’s massive Saddle fire, a drone prevented firefighting planes from taking off—if the planes had been able to attack the fire from above, people would not have needed to be evacuated, according to Utah governor Gary Herbert. So far, in 2017, there have been 17 incidents of unauthorized drone disturbance in wildfire areas. In 2016, 40 such occurrences were recorded. In Colorado, firefighting crews are figuring out the most effective ways to use authorized unmanned aerial systems (UAS) to aid fire suppression tactics. When used in an official capacity, drones can be extremely useful. They can be used to survey landscape during a lightning storm when manned aircraft are grounded, or they can be used to deliver supplies to ground crews working in remote areas. Further, with new infrared technology, drones can be used to essentially automate the response protocol process to identify fires with the greatest threat potential, and dispatch the necessary resources before the fires explode out of control. Other leading-edge UAS applications for firefighters include drones that can be pre-programmed with Google Maps flight plans prior to launch, or drones that can stay in the air for hours with greater line-of-sight communications than ever before. The true difference between unauthorized and authorized UAS in wildfire fighting situations is the communication capabilities. When deployed correctly, authorized UAS can use TDMA technology to communicate with other aircraft in the area and ensure that no collisions or interference incidents occur. TDMA is a frequency channel access technique for shared communication networks, essentially enabling a more sophisticated way to drive Point-to-Multipoint communications. It allows multiple transceivers to access and share a single radio frequency channel without interference by dividing the signal into different transmission time slots. This enables swarming applications that enable multiple unmanned systems to operate autonomously, in tandem. For many personal drone users, the temptation to use this emerging technology to capture images or video is strong. Better cameras, greater operating distances and stronger communication capabilities have created a tool that can be both fun and useful for the average user. However, for wildland firefighters, the use of these unauthorized drones pose a serious threat to both their safety and the safety of the civilians they are tasked with protecting.
The Importance of Frequency Hopping
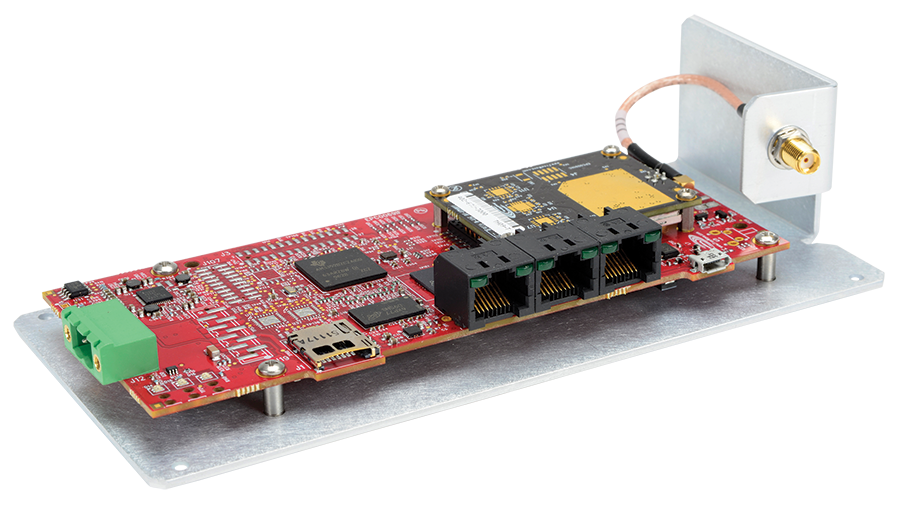
(Original blog can be found on the Texas Instruments website) Are you a fan of those 1940s black-and-white movies where a damsel in distress gets rescued by a rough-and-ready private eye? If so, then you’ve probably seen actress Hedy Lamarr. In real life, Hedy was no damsel in distress. She was one of the primary inventors of frequency hopping technology now seen in Wi-Fi®, Bluetooth® and code-division multiple access (CDMA). The technology Hedy Lamarr helped invent is frequency-hopping spread-spectrum (FHSS) radio technology. FHSS is a wireless technology that spreads signals over rapidly changing frequencies. Each available frequency band is divided into subfrequencies. Signals rapidly change, or “hop,” among these subfrequency bands in a pre-determined order. Used in global industrial applications for over 60 years, 900MHz FHSS radios equipped with TI’s chipsets like the SimpleLink™ Sub-1 GHz CC1310 wireless microcontroller (MCU) now have the ability to host process-automation apps for the intelligent command and control of remote sensors and devices. Without having to leverage expensive Wi-Fi bandwidth, lay fiber or employ cost-prohibitive cellular, companies can now take advantage of proven low-power FHSS technology to automate processes at the network edge. The proliferation of smart sensors and high-bandwidth devices makes low-power FHSS technology a viable and cybersecure wireless data option for oil and gas, unmanned systems (like unmanned aerial vehicles [UAVs] and robots) and original equipment manufacturer (OEM) wireless integration. Because innovators like TI have developed such powerful chips, FHSS is no longer restricted to pure telemetry or input/output (I/O). Indeed, FHSS increasingly supports voice and video, and can scale to form self-healing mesh networks. Moreover, FHSS transmits data over much longer distances than Wi-Fi, Bluetooth, LoRa or zigbee – up to 60 miles in some cases. Because FHSS is a wireless technology that spreads its signal over rapidly hopping radio frequencies, it is highly resistant to interference and is difficult to intercept. Interference at a specific frequency only affects the transmission during that extremely short interval, making FHSS inherently cybersecure. By employing intelligent TI-based FHSS technology, organizations can take advantage of real-world fog computing and intelligent edge communication devices that are cybersecure and resilient. When deployed as process-automation nodes, these devices (pictured in Figure 1) can make decisions and take action at the access level (or at the sensor or device). Indeed, not only is FHSS a reliable and robust option for Internet of Things (IoT) networks, it is also a low capex and opex solution that can work for years without maintenance. Contact FreeWave to learn more about FHSS technology and order a couple of TI-powered radios that you can program (in Python, Node-RED and Node.js) for real-world fog and edge applications. Also, find out more information about the CC1310 wireless MCU and other products within the SimpleLink MCU platform.
Rugged IIoT Solutions That Can Weather Any Storm
Mount Washington Observatory (MWO) is a research facility located at the heart of what many consider the “home of the world’s worst weather.” Think thick ice, dense fog, drifting snow, powerful winds, sub-arctic temperatures, rapidly changing conditions and more fog. The New Hampshire-based facility provides critical research data on the Earth’s climate and doubles to protect the lives of the MWO crew, US Forest Service Snow Rangers and New Hampshire Fish and Game employees by providing real-time weather updates. Collecting data is critically important for MWO operations and the safety of those it helps protect. In this vicious and unforgiving environment, FreeWave’s rugged IIoT solutions are responsible for delivering the data that is invaluable to research and safety efforts. Powering through Fog and Ice The extreme conditions at the MWO facility range from fog with 50-100 mph winds to sub-arctic temperatures that are accompanied by 140+mph winds and thick ice. The weather is known to change frequently and fast, with ice accretion rates of up to 12” per hour — and visibility is often limited or non-existent. These extremes make it the ideal location for studying the environment and climate. However, when search and rescue teams are deployed the situation can quickly become dangerous. They rely on MWO’s real-time data to assess conditions. As you can imagine, there is little room for connectivity issues when people are out in the elements. Ruggedized IIoT Solutions The key to establishing a network at Mount Washington is robust and hardened technology that will perform in the Summer and Winter extremes. For more than 13 years, FreeWave 900MHz spread spectrum radios have delivered the data that the crew relies on to survive some of the most intense weather in North America. While the technology is constantly exposed to the rough conditions, it performs day-in and day-out, providing critical data around the clock. Check out the full case study, including a description of the network here: https://www.freewave.com/mount-washington-observatory/
Manufacturing Change through Big Data, Predictive Maintenance & Remote Access
Although the manufacturing industry has seen some troubling times over the past few decades, new technologies are helping it make a resurgence. So what has manufactured this change, you might ask? The rise of automation and robotics across many sectors, and perhaps one of the most significant industrial impacts since the assembly line was created – the Internet of Things. IoT has given rise to advancements in sensor technologies and M2M (machine-to-machine) communications, along with edge computing analytics and business intelligence from big data. These new methods are fundamentally changing the way goods are designed and produced. We recently wrote a blog highlighting some of these impacts and challenges that coming along with it. Below, however, we’ve gathered a handful of recent industry news articles for you to explore and learn how the industrial IoT is changing the manufacturing landscape as we know it. The Hunt for Zero Defective Parts Per Million When it comes to highly scrutinized and regulated industries, automotive manufacturing is near the top of the list. Understandably, then, automotive manufacturers are quite keen on the pursuit of zero Defective Parts Per Million (DPPM). This recent article from Manufacturing Business Technology discusses the driving forces behind this movement, namely the advent of autonomous vehicle technology. While on-vehicle computer systems of the past may have controlled entertainment or emissions systems, in the near future almost every vehicle system will rely on a piece of silicon in one way or another. With the stakes higher than ever, the advanced capabilities of the IIoT are coming into play to drive manufacturing processes. Moving Outside the Plant: Remote Access Is Quickly Evolving Just a handful of years ago, remote access technology was not a standard. However, as noted in this article from Automation World, a recent survey discovered that 72% of respondents are using remote access to monitor plant equipment and data. While the usage of remote access does vary by industry, the growth in this segment of the IIoT has been strong and shows no signs of slowing — and the applications for remote access are diverse. As Matt Wells, GM of Automation Software for GE Digital said, ““Anyone dealing with distributed fleets has a strong demand to be able to see, manage or control it from a remote spot,” he explains. “It all comes down to the difficulty of accessing that remote asset.” Big Data and Shale 2.0 As oil prices seem to have stabilized (for now) at a lower new norm, oil companies are having to get creative to keep margins healthy and profits rising. One of the ways companies are accomplishing this is through Big Data and the IIoT. This article from E&P Magazine highlights some of the challenges and hesitancies that are emerging within the industry, often fueled by cultural difficulties. However, Mark Slaughter — longtime Halliburton employee and current venture capital advisor — believes in just 10 years, smart analytics will give oil companies the ability to produce the most economic barrel of oil. Preventing Machine Failures through A.I. Automotive recalls are a massive expense for car manufacturers, not to mention the significant public relations disaster that can arise. In an effort to avoid this expensive and unseemly events, automotive companies are turning towards next-gen analytics and automation technologies to help prevent this issues before they become widespread problems. This article from IT Brief states that a recent McKinsey study shows that predictive maintenance could save global businesses an incredible $630 billion a year by 2025. In a world where recalls are pricey PR nightmares, this is music to automotive manufacturers ears. The IIoT’s Role in Product as a Service and Predictive Maintenance Models This recent article from Plant Services explores how the IIoT is changing the way equipment manufacturers and service providers approach their business, particularly through Product-as-a-Service (PaaS) and Predictive Maintenance (PdM). PaaS is the idea of charging for the output of a piece of equipment, rather than an upfront fee for the equipment itself. For example, the volume of compressed air generated by an air compressor. With PdM, advanced analytics are used to monitor the various systems in a piece of equipment, and diagnose and fix potential issues before they become larger (and more expensive ones). As the IIoT continues to grow, and more applications become mainstream, it will be interesting to see how manufacturing processes adapt and change. What new manufacturing promise do you think the IIoT holds? Where industry do you see IIoT gaining a foothold in next?
Manufacturing in the Age of IIoT
Few industries can claim such a foundational impact on the United States as the manufacturing industry. Modern manufacturing began with the birth of the assembly line and the transformational effect it had on the automobile industry. Companies then adopted that approach to product manufacturing and logistics. The early phases of the next generation of manufacturing appeared as machine-to-machine (M2M) communication, a forbearer of the concept behind the Internet of Things (IoT). Eventually, IoT became so broad that specific designations were needed to differentiate between the consumer and industrial side of things, thus paving the way for the Industrial IoT (IIoT). Today, manufacturing companies, while often on the leading edge of automation technology, are still scrambling to adapt to the explosion of sensors, communication platforms, big data and high-speed analytics to maximize efficiency and future-proof their products or designs. Some companies are touting the idea of retrofitting – a concept that has existed for some time – but some plant engineers may be wary of the need for continual updating to a system that is bound to become irrelevant at some point. Still, the process can be relatively painless, and is quickly becoming necessary, as Plant Magazine notes: … Most food manufacturing and processing plants have motors powering essential equipment such as mixers, conveyors and packaging machines. But they’re just motors. They don’t play in the same league as other intelligent devices. With years of service to go, it’s difficult for plant managers to justify replacing motors that work just to make an upgrade with smart features. But motors can connect to the IIoT without a complete overhaul. Instead of investing in new, more intelligent/smart equipment, consider investing in sensors that provide similar functionality to connected devices. Smart sensors attach to almost any standard low-voltage induction motor. Sensor technology is sophisticated enough to be small, functional and energy efficient. For certain kinds of manufacturing plants, a complete overhaul may not be necessary, and a ‘simple’ retrofitting process might easily solve the first part of the problem. The second part of the problem, or challenge, is that along with smart hardware, plants also need the software and data processing capabilities to keep pace. Some plant engineers are solving these challenges by deploying programmable radios capable of hosting third-party applications so that the data can be transmitted in smaller, highly specific packets, making the transport both fast and easier to push into predictive analytics platforms. From there, software companies are building in the ability to process data in the cloud, essentially running all critical data and software operations through either a fog or cloud computing process. Cloud software services have the potential to be highly customizable based on the needs of the manufacturing plant. These technologies are good examples of the ongoing convergence between traditional information technology (IT) and operations technology (OT) needs in industrial markets. Currently, the manufacturing industry is sitting in an interesting spot: leaders in the M2M world, but still adapting to the IoT world. Where the industry ends up in the next 10 years could be a strong indicator of the economic and financial temperature of the domestic and international marketplaces.
Happy Independence Day!
As we prepare for fireworks, barbeques and all of the excitement that comes along with tomorrow’s holiday, we’d also like to recognize what Independence Day means to the U.S. By definition it’s the celebration of the Declaration of Independence and the birth of our incredible country as an independent nation. On this holiday, we’re also reminded that millions of people have sacrificed (and continue to sacrifice) in order for us to gain and retain our freedoms and liberties. As a company that has had the honor of working in the military and defense industry for more than two decades, we are humbled and grateful to all of the men and women in the armed forces. From the bottom of our hearts, with respect and admiration, we’d like to thank all of brave men and women who have served and sacrificed for this great country — including those who are currently serving today. FreeWave and the Military The government and defense industries have been woven into FreeWave’s story from early on. As previously noted, we have worked in the defense markets for more than two decades providing wireless communication solutions – including command and control (C2) links for unmanned systems. Our embedded communication solutions for drones and robotics have logged more than 2.5 million flight hours without a single link failure. As the number of unmanned systems for air, land and water increases, it is imperative for manufacturers and operators to use rugged, reliable and secure C2 solutions with high-speed data transmission. We are dedicated to continuing to provide robust and trusted solutions. Not only do we focus on providing a great technology, but a solution that can be trusted to operate when human lives are at stake. We hope you have a wonderful Fourth of July holiday!