Ranch Life: Water Visibility is Critical Part 1

There is no average day in the life of a rancher. Many kickstart their morning at 4 a.m., when most people are still fast asleep. After breakfast, the real work and the long day begins. It might include mending fences, checking grass levels across thousands of acres, rotating cattle or even being called unexpectedly to tend to a neighbor’s sick animal. All this is done by riding the land or rolling out trucks in hard-to-reach places with little or no cell coverage – and so much connects back to water. From land and hay operations to logging and livestock operations, water conservation touches almost every aspect of ranch performance and profitability. Take JJ Goicoechea, for example, who travels at least 40 miles a day (one way) to check on the viability of the water on his land for the surrounding cattle and wildlife. Or Bob Skinner, who used his own funds to purchase an airplane as a means to check on his pipelines every 48 hours. These examples, courtesy of the Public Lands Council, show observation and measurement for better on-ranch performance is nothing new for ranchers. What has evolved is how the modern rancher observes and measures today with near real-time visibility, particularly when it comes to water management. Water Becomes a Commodity It’s no secret that water is a rancher’s most valuable asset. Safe, clean, abundant water sources are necessary for the health of the herd. Water impacts the profitability of ranch operations, many of which were handed down from previous generations. There’s a new challenge, though, that the men and women who homesteaded the land did not have to contend with: extreme weather and unreliability of water sources. Case in point: 2012, when two-thirds of the lower 48 states were in a drought. Or earlier in 2022, when according to the U.S. Drought Monitor, more than 32% of western states, including Texas, Utah, Oregon, and New Mexico, were in a severe drought – the worst megadrought reported in 1,200 years, according to Scientific American. With the unpredictability of nature and the need to conserve reliable, clean sources of water, a better, more efficient way to store and sustainably save water is surely needed. What if You Could See the Entire Ranch on Your Device? Just like their forefathers, a rancher’s keen eye for observation and measurement serves them well. There’s a gut check to making decisions, and experience guides the way. That will never change. The modern cowboy, however, is evolving in one significant way: they can now see their entire ranch operation in real-time on a connected device: cell phone, tablet, laptop or desktop computer. Here is how near real-time visibility – being able to see the different parts of a ranch without physically being there – works. Sensor technology “carries the water” for ranchers and farmers, helping them visualize what’s happening across thousands of acres without having to physically roll out trucks. These devices, or “things,” then relay data back to ranchers so they can make informed decisions based on near real-time visibility. It’s like having extra “eyes and ears” spread across the ranch. In short, these connected devices are the Internet of Things (of the ranch) or IoT, for short. FreeWave provides a drop-in solution – our Tank Level Monitor – that’s easy to install, set-up, and manage. For any of us, you don’t know what you don’t know. For ranchers, this knowledge gap comes with a price as rising fertilizer, equipment, and input costs squeeze margins. Every unexpected cost is closely watched. A dehydrated calf in peril costs more than a thousand dollars to replace. A blown tire on a truck shows up on the P&L. Man-hours spent checking water levels and the status of equipment add up. When it comes to water consumption, IoT is making a difference. According to a research report conducted by Transforma Insights and 6GWorld, by 2030, connected devices and the information they impart will help conserve close to 230 billion cubic meters of water. What does that even look like? Here, we turn to beer to help us out. Considering 40 million cubic meters of water is equal to about 300 billion pints, IoT is predicted to save the same amount of beer consumed at Oktoberfest in Munich for two straight decades. That’s a lot of water saved. While 35% of those savings will come from smart water grid operations, the remaining 65% will be driven by “IoT-enabled agricultural operations like crop management and remote pest control,” according to the report. What Observing and Measuring Means Today Connected devices save valuable time, money, and resources. They give ranchers “eyes and ears” into their entire operation and support what these stewards of our land have always done well: observation and measurement. Modern ranchers are using technology to ask – and answer – critical questions about the status of physical assets, water tank levels, water flow, weather, and soil, like: Do the stock tanks have enough water to keep the livestock healthy? Is there excess water in the soil that will lead to ponding? Are we irrigating the hay fields with too much or too little water? Are equipment like livestock trailers and tractors running smoothly? What’s the condition of remote pumps – are they working, is there a leak, is the herd getting what they need when they need it? A long-held rule for ranchers is that they don’t quit when they’re tired, they quit when they’re done. We aim to support ranchers in getting more of the right things done – with less water, waste, and worry. Talk to FreeWave today and see how our solutions can help you save time, energy, and money with a drop-in solution that just makes sense.
The Impact of IoT on the Future of the Oil and Gas Industry
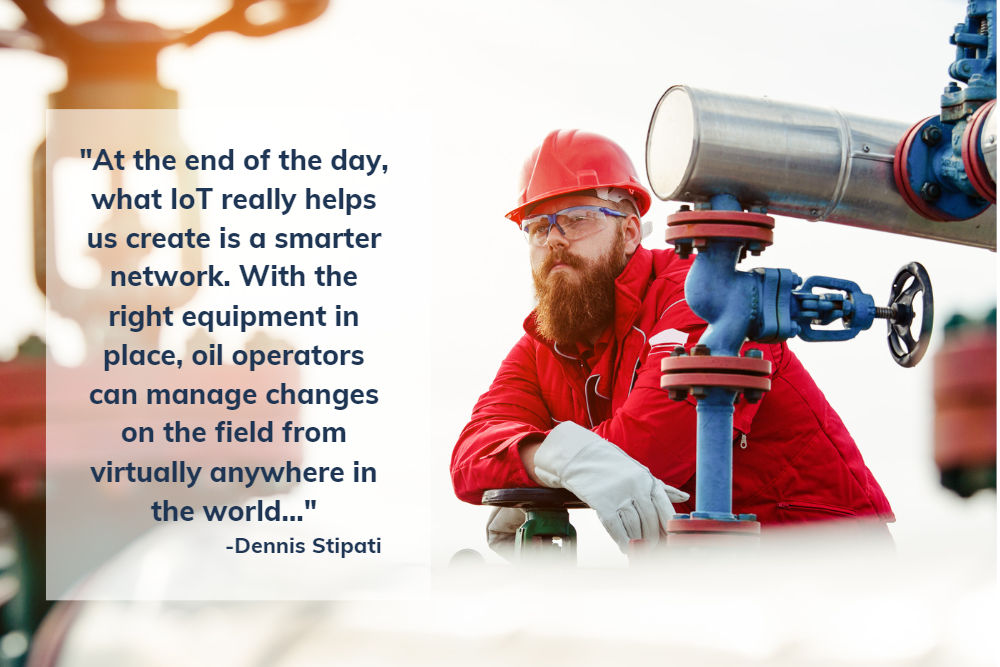
A global expert in telecommunication, Dennis Stipati talks about how today’s energy companies are doing more with the same amount of resources and how FreeWave sees the future for smart oil fields. A true industrial transformation is taking place as we speak. Connected devices delivering data to technicians and managers through the internet – what we all know as the Industrial Internet of Things (IIoT) – are transforming efficiency and productivity for forward-thinking energy companies. Oftentimes, wells are located many miles apart in extreme weather conditions or might even be offshore on an oil rig. Through digitalization, oil and gas leaders are implementing innovative strategies to do more with the same amount of people and resources while increasing overall safety and environmental sustainability. Here, we explore the impact of IIoT in the oil and gas sector with FreeWave’s Senior Director of Strategic Accounts, Dennis Stipati. Q: The Industrial Internet of Things (IIoT) is significantly impacting every industry; what are the top problems IIoT is solving for energy companies?? Dennis: From the operations side of things, being more efficient and increasing revenue is huge. Over the last year or two, there’s been a lot going on in our world. There’s not enough gas, not enough oil, and on top of that, we’re trying to get the oil and gas that we do have to the right places. That’s where IIoT steps in, helping us increase revenue and improve efficiency within operations. For example, if a drilling rig is down for a short period of time, that oil company could lose millions of dollars, potentially. It’s important to be able to remotely control the different sensors on that oil rig so that downtime is decreased and productivity and overall revenue is increased. That’s one benefit. On the other end, IIoT also impacts the overall safety of workers on the field and the surrounding environment. In the past, oil operators weren’t able to get the type of detailed operational information that we have access to today, and this data makes a big difference in reducing safety hazards on the field. With the right equipment in place, we can see when machine parts need to be replaced before their end of life. We can also virtually measure the amount of oil that’s coming through the pipelines and see if there are any leaks or dangerous chemical exposures before a crisis arises. IIoT also helps us control the day-to-day management of our operations from anywhere in the world, which leads to greater sustainability. Say there’s a methane leak of some sort. We can now respond to a situation like this immediately instead of after hundreds of thousands of gallons have been released into the environment. A decrease in environmental hazards means a safer and more sustainable world for all of us. At the end of the day, what IIoT really helps us create is a smarter network. With the right equipment in place, oil operators can manage changes on the field from virtually anywhere in the world, no matter if it’s a change flow, tank pressure, or even the temperature. With a smarter network, these decisions can be made on the edge. Q: How does the use of IIoT in the oil and gas industry impact the everyday person? Dennis: IIoT in oil and gas is important for a number of reasons, but the biggest thing most people pay attention to is gas prices. Whether it’s filling up their car or paying for natural or propane gas, this is an industry that affects all of us. It’s important for oil operators to be as efficient as they can so that they can make a profit and then pass along those cost savings to everyday consumers so that we can continue to do the things that make up our daily lives. Q: What FreeWave products are currently being used in the oil and gas industry? Dennis: It seems like every day, a new app is invented to help make our lives easier. I think FreeWave products function in the same way. Our IIoT solutions, including Zumlink™, ZumEdge®, Fusion™ Bridge radios along with our FreeWave Edge software platform, help our customers operate with greater efficiency and make better decisions on the edge. We currently have our products right on the drilling rigs. A lot of times, these platforms are fairly large, and they’ll have five or six radios on a drilling rig, maybe even more, that are wirelessly interconnected. Our products are also used on the pipeline to measure the flow of the natural gas going through that pipeline as well as the temperature. Some of our radios are used in the terminals to connect a tank to the back office or monitor a fracking pond to make sure there are no leaks. Honestly, I feel like every week, I learn a new way a customer uses our products. You think you know it all, and then someone else comes back and shares a different way they are using our solutions within their remote operation. Q: As you look at the future, and the role of IIoT within it, what excites you the most? Dennis: The common theme I keep seeing in technology is automation. Our population here in North America and even in Europe is decreasing. Recently, I read a report that said there are two jobs available for every person that’s looking for employment. How do we fix that? Automation. The more we use IIoT, the more we can make better decisions without human intervention. Machine learning, autonomy at the edge, and computerized systems, these things all make a big difference in the day-to-day management of our operations. I think we forget just how much more efficient and productive our lives are today because of technology. When I look at my life and think about the evolution of basic TV to streaming services or the transformation of the bag phone to the iPhone, I’m really amazed at how far we’ve come in such a
Technology Simplified: Leveraging Data in the New Digital Era
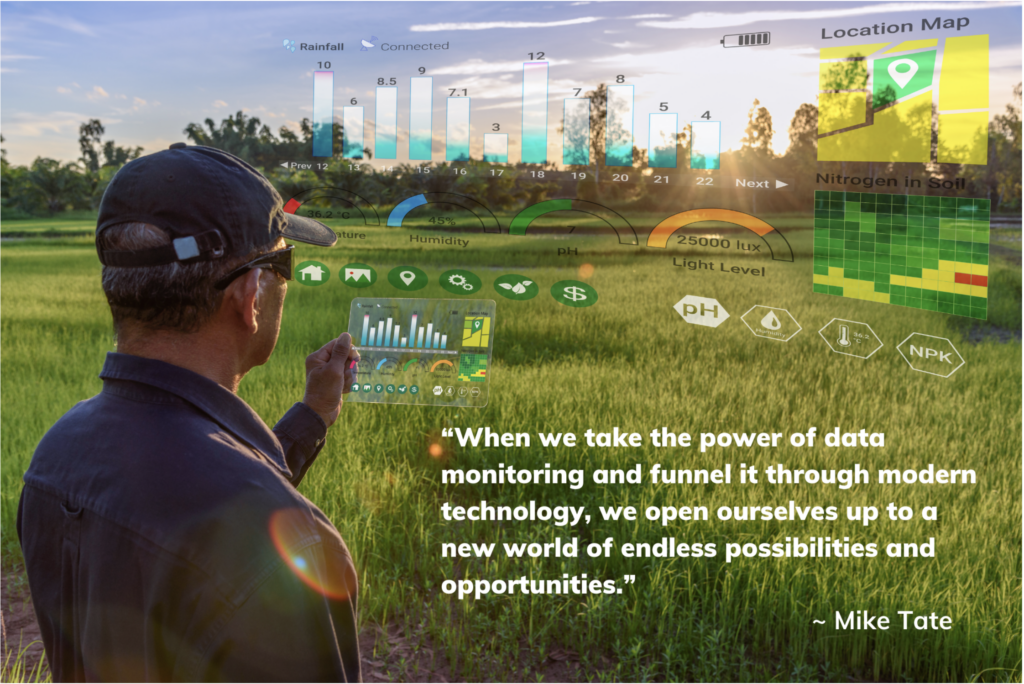
Excited by tomorrow, we face a new world filled with endless possibilities each day. Thanks to modern technology, simple sensors open the doors to our favorite restaurant, edge computing allows manufacturers to spot and correct production glitches before they happen, and high-tech traffic cameras analyze and record thousands of license plates daily to spot stolen and unregistered vehicles while also identifying suspected criminals. It’s no secret that the world is evolving before our eyes, and through the technological advancements of this digital era, we are creating a more efficient world. The power of data Data is a powerful tool of knowledge, and lucky for us, it’s everywhere! Every one of our actions is driven by a manual process of data – like the simple act of putting on a jacket when it gets cold, or an automated process of data – like a valve instinctively shutting off when a water tank gets full. Today we have the technology to effectively process, analyze and distribute data metrics in tremendously impactful ways. What does greater simplification look like for industrial leaders? Remote operations simplified When leveraged effectively, industrial internet of things (IIoT) solutions take remote operations to the next level, simplifying the work process for teams and industries across the globe. Think about some of the most popular high-value remote assets today, like drones, video surveillance, or even center pivot irrigation systems – these entities perform so well because they do what humans can’t. In mere seconds, IIoT technology can process, distribute and respond to data that would otherwise take an entire team hours, days or even weeks to achieve. In the not so distant past, industrial operations relied solely on data consumption (i.e., how much water is in the tank; what temperature is the water), but today, advancements give us the ability to respond nearly instantaneously to that collected data with actionable execution. Today we can view and control the management of an entire operation remotely on our cell phone. We can see how much water is in a tank or what temperature that water is at and automatically change and adjust the water levels and temperatures from near or far. As a result, the amount of time, resources and energy needed to run businesses has transformed entirely, and this evolution allows us to create an enhanced world and standard of work. Simple deployment Remote operations are oftentimes in rugged terrain, making them difficult or even impossible to access. At FreeWave, we solve this complex issue by providing pre-configured ready-to-deploy solutions, complete with everything needed to achieve the mission at hand. For example, through FreeWaves’s joint venture with ModuSense, we’re simplifying connectivity to cloud with a variety of pre-configured and ready to deploy monitoring and sensing solutions by supplying the entire solution with a 12-month data plan, dashboard, 12W rapid recharge solar panel, satellite connectivity and Bluetooth connectivity. You can use your mobile phone to validate the data directly from the gateway without having to wait for satellite transmission. We all know the “gotchas” when it comes to buying technology. Simple deployment means you’re ready from day one, without needing to buy additional components. Real-world impact As Chief Operating Officer and SVP of Global Sales and Marketing at FreeWave, I get a front-row seat to the real-life impact modern-day technology is having on lives, businesses and entire industries. The essentials of life have become simplified, and in the process, more people and businesses receive greater access to the things that matter most like critical information, metrics and potential outcomes. Creating a more sustainable world and preserving natural resources like food, air, energy and water have been at the forefront of IIoT since FreeWave began almost three decades ago when we brought long range, low power consumption, C1D2, 900 MHz connectivity and radio technology products to our customers. Since then, our connectivity options have greatly expanded by adding EDGE Compute, Software, Industry Protocol Conversions, Data Broker & Cloud, a complete end to end solution and with it comes the responsibility for greater environmental stewardship. We’ve all seen the devastating impact an environmental catastrophe, like the 2010 Deepwater Horizon oil spill, can have on the globe. Simple mistakes can and do cause enormous repercussions that affect us all. The truth is, with human interaction there will always be the cost of time and possible room for error. Technology, however, is different, as it allows us to not rely solely on human capacity and depend more on interconnected and advanced systems. Now, we don’t have to wait for someone to run into a situation or crisis and manually pull a lever or travel to turn off a valve. Instead, preprogrammed automation or a simple click of a button or flip of a switch from virtually anywhere in the world can control your high value remote assets. FreeWave is a technological pioneer in the 21st century. We have connected the unconnected with a reliable ecosystem of edge intelligent radios and solutions to optimize the extreme edge of remote industrial operations. Through our single IIoT platform, we provide expanded capabilities for data capture, analysis, control and automation. Our single pane of glass approach provides a simple, single vendor, one-stop-shop solution for remote operations worldwide. At the end of the day, when we take the power of data monitoring and funnel it through modern technology, we open ourselves up to a new world of endless possibilities and opportunities. It’s one thing to have data; it’s an entirely different thing to know how to leverage that data. At FreeWave, we are constantly pushing the boundaries of data monitoring and modern technology through our IIoT solutions and creating a better, safer and faster world of work for industries around the globe.
Automation in Oil and Gas: A Starter’s Guide
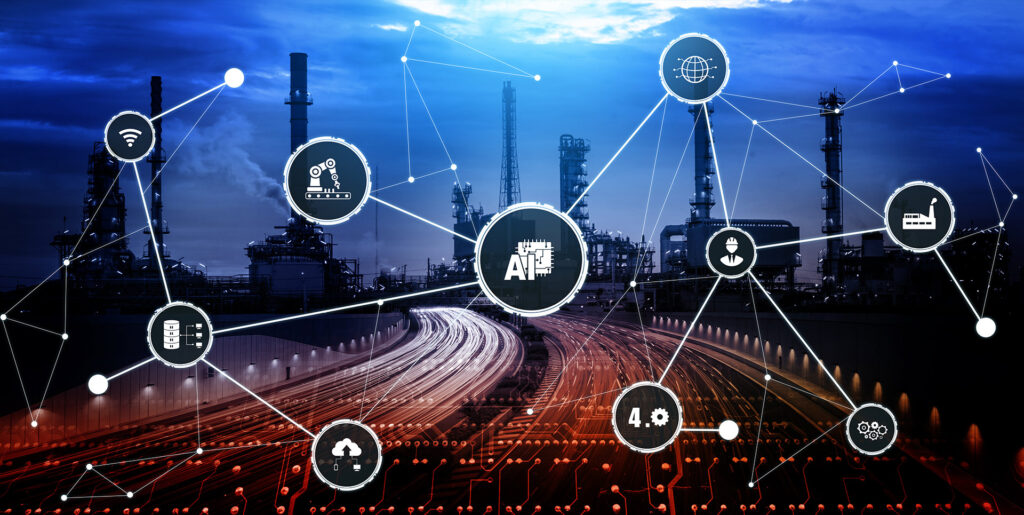
From drilling to logistics to preventing theft, automation in oil and gas is quickly becoming the standard. Learn how tech helps increase ROI and improves safety in this starter guide. Since the 1990s, businesses have looked at how automation in oil and gas can improve worker safety, improve efficiency, and increase the bottom line. Today, digital tools are being used in every facet of oil and gas cultivation. From improved efficiency when drilling for new oil to real-time weather monitoring and theft prevention, tech tools are quickly becoming the norm for the $2.1 trillion (according to IBISWorld) industry. In this starter guide, you’ll learn how innovation and automation in oil and gas is being used to connect, collect and analyze data, and increase ROI. What Is Automation In Oil and Gas? Oil and gas automation refers to the growing number of digital techniques and processes used to help producers cultivate energy. Automation and agility have found their way into nearly all oil and gas industry divisions, like drilling, logistics, supply chain, and safety. Tools such as rugged wireless radios and AI-powered real-time sensors for remote monitoring allow drilling sites to be run safely and efficiently from afar—protecting employees and increasing revenue simultaneously. Benefits Improved production yield while lowering costs Improved safety for employees in hazardous conditions Real-time insights 24/7 monitoring Theft protection at drill sites and along pipelines Sustainability Predictive technologies can be used for future application Where Does Automation In Oil and Gas Happen? Approximately 94 billion barrels of oil are produced every day worldwide, according to U.S. Energy Information. Here are some specific examples of how automation impacts the production and monitoring of two of the world’s most important resources. Drilling Autonomous drilling control systems (ADCs), such as those implemented in the North Sea (between England and Scotland) in 2020, enable safe and efficient oil drilling. In the past, “automatic” tools used to drill for oil were just manually assisted. Today, though, ADCs are believed to reduce drilling costs by as much as 50 percent. Diagnostics In an industry where downtime can severely disrupt a business and lead to financial downfall, remote diagnostics help predict future issues or pinpoint current ones to prevent delays and disruptions. For example, tools that measure pressure loss, temperature, and mercury levels can help businesses disrupt downtime and minimize costly delays. They also reduce the risk of oil rig disasters, such as the infamous Gulf of Mexico explosion on the Deepwater Horizon oil rig that left 41 miles of oil in the ocean. Weather Monitoring Oil and gas production are both contingent on weather patterns. Issues that can affect (or even shut down) drilling sites include: Tropical cyclones (most common) Extreme cold Extreme heat Earthquakes Automation in gas and oil includes the adoption of real-time sensors and monitoring tools, which detect changes in seismic activities and atmospheric levels, giving companies the ability to adjust in real-time to changing weather patterns. Security Theft in oil and gas is a real threat. In fact, a 2021 report said that Nigeria loses an average of 200,000 oil barrels per day (b/d) to theft, primarily from pipeline sabotage. Rugged, wireless radios allow oil and gas professionals to communicate safely without fear of interception or lost connection. Along with real-time monitoring of sites and pipelines, this can create a formidable defense against criminals. Trends in Oil and Gas Automation Oil and gas automation is quickly becoming standard, and with it, innovation in the field is coming. A significant push towards sustainability. Tech tools that help reduce a business’s carbon footprint and improve operating efficiency will be both sought after (and possibly required) in the coming years. Greater use of AI at oil rigs. Businesses are shifting away from manually assisted technologies in favor of artificial intelligence devices that make real-time, autonomous decisions on-site. More tech jobs. As on-site employees are phased out to make for a safer work environment, new jobs, such as coding, system architecture, and cybersecurity, will be created in the oil and gas industry. Contact FreeWave to learn how our technologies can boost your oil and gas business’s ROI today.
9 Critical Reasons to add Wireless Thief Hatch Management
A thief hatch is a closeable lid at the top of a low-pressure holding tank for hydrocarbons such as oil or condensate, or water. It allows access for measurement, however, if left open it can allow hydrocarbon vapors to escape into the atmosphere as fugitive emissions. Hydrocarbon tanks are almost always Class 1 Div 1 hazardous locations. If your thief hatch pops open from overpressure conditions, or if an operator accidentally leaves it open, you could be in violation of strict air pollution compliance rules on fugitive emissions. The Colorado Department of Public Health and Environment (CDPHE) Regulation 7, Section XII, “Volatile Organic Compound Emissions from Oil and Gas Operations”, requires facilities to control venting of natural gas from many oil and gas emission sources. The CDPHE has determined that improperly secured thief hatches, visible emissions from a flare, and audible emissions from a thief hatch or pressure relief device (PRV) are violations of Regulation No. 7. Many of the 23 oil producing states (including Ohio, Utah, Wyoming) are looking at the CDPHE rulebook as a possible blueprint for their state rules. The minimum fine by CDPHE for an open thief hatch, visible emissions from a flare or audible emissions from a thief hatch or PRV is $15,000/day. The duration of each fugitive emission violation is assumed to be at least one day unless evidence gathered by the CDPHE and/or provided by the source proves otherwise. The USEPA’s new regulations affecting methane (CH4) and VOC emissions from the oil and gas sector became effective August 3, 2016. Updates to NSPS OOOO list storage thief hatches as one of the fugitive emission leak components that will be periodically checked for leaks using optical gas imaging (OGI). Thief hatches are usually easy to see and make easy pickings for regulatory compliance inspectors. Inspectors will often check thief hatches first, and use them as indicators of other violations for a site. Open thief hatch detection is a powerful tool to minimize fugitive emissions. Most solutions on the market to detect an open thief hatch are wired and expensive to install and integrate into an existing SCADA system. FreeWave delivers an inexpensive and easy to deploy Class 1 Div 1 wireless solution for Thief Hatch Monitoring with the WC30i-AXIS Angle Sensor. FreeWave’s new WC30i-AXIS Wireless Angle Sensor is a solid-state inclinometer that measures the opening angle of a Thief Hatch and reports as closed, cracked or open. It links wirelessly to the WC45i Gateway, which communicates to the PLC or SCADA system with Modbus communication protocol. Together with the WC45i Gateway, the WAVECONTACT system is easily and quickly deployed to implement industrial automation where wired installations are cost prohibitive. The WAVECONTACT System has been designed for deployment in Class 1 Div 1 locations. Contact Sales to Learn More
Injecting Agility and Automation at the Well Pad
Small-to-medium-sized oil and gas companies understand what it takes to be agile. They must survive and thrive in an industry led by giant producers. While no recipe to success is the same, the smaller players need to maximize production while simultaneously keeping costs down if they want to compete in the market. By adopting technology solutions that will make them agile and effective, these organizations can secure fast and significant ROI, while meeting production and operations demands. However, technology selection in a constantly changing landscape is murky at best. Take an operations manager at a small oil and gas company, for example. They are likely tasked with ensuring that operations are running smoothly at the wellhead while delivering critical data back to the business office in real time. It seems simple enough, but the operator is probably facing constant pressure to provide insights into their production sites and new solutions for operational efficiencies. At the same time, the IT team wants monitoring at the well pad 24/7/365, and they want to access that data whenever they please from anywhere. Perhaps, they have attempted to tack on several different technology solutions to help provide said data – but the new demands require a more sophisticated approach. The pressure is on to find a way to optimize data collection, monitoring and control of the assets in the field (including the communications network) or the company won’t be able to compete with the “always on” oil and gas producers. The good news is that there is hope. There are programmable wireless communication solutions for the well pad that are available today. With a little research, it is possible to find a rugged, easy to use solution that will deliver massive ROI. What Does Well Pad Automation Look Like? In modern oil and gas operations, well pad automation builds analytics and intelligence into the wellhead environment. This takes a step beyond traditional communications because it enables intelligent applications and programmability that establish an advanced operating environment. Automation can also present the opportunity for predictive analytics, remote command and control, new protocol translations, and modern cloud-based services at the wellhead. Automation helps an operator streamline their job and provides the IT decision makers with data that helps them understand daily operations. Automation technology makes this possible by powering data transmission, improving data quality and enabling intelligent data analysis. The oil and gas company then has the power to make informed decisions that drive higher production outputs, with ROI often achieved in a matter of months, along with substantially lower CAPEX. Bringing an Automated Monitoring System All Under One Roof The financial and business benefits of industrial automation are clear, however selecting technology solutions can be challenging. Operations managers need a wireless communication solution that can support next generation of well pad automation needs. The solution must include a combination of data monitoring, logic execution and data visualization. This is especially beneficial at the well pad sites that are remote and isolated. The big advantage today is that these decision makers are no longer limited to disparate technology solutions: Wi-Fi Automated Monitoring Systems establish Wi-Fi at the wellhead to enable voice, video, sensor data access and perimeter security. They can also leverage Wi-Fi for rapid maintenance across the wellhead, saving maintenance staff hours of time. Instead of driving to the remote wellhead, they are now troubleshooting issues from a truck or office. Wi-Fi also supports the collection of information from RFID devices and wearable devices designed to protect workers in the field. FHSS When the Wi-Fi is bridged with a Radio Frequency (RF) solution, particularly Frequency Hopping Spread Spectrum (FHSS) technology, the data can then be collected from tank farms, PLCs, and sensors on the well and within the well. The wireless intelligence that is located on the devices in the sensor network, enables local execution on the RF devices, which supports data storage or data collection and analysis. Through cloud-based services, the data can be published globally, allowing mobile access from virtually anywhere. Additionally, an automated monitoring system may enable wireless telemetry in hazardous environments through modular wireless I/O solutions that leverage sensors to monitor specific points along the wellhead. Programmability With built in programmability on top of Wi-Fi and RF technology, the automated monitoring system is not only optimizes today’s operations, but it prepares the organization for the future as industries shift towards digital technology and total connectivity. For example, an engineer can write a simple application using open source technologies like Node-RED and Python that will display a dashboard of real-time data from the well pad as it collects information from sensors. The organization could also automate tank-level monitoring by developing or leveraging a third-party application to monitor water levels in the remote tanks from the cloud – which would then be accessible anywhere with a wireless internet connection. Benefits that Stretch Beyond ROI Automation at the well pad not only leads to ROI through wireless automated monitoring and control, but it has the power to transform operations and streamline production. When a small-to-medium-sized oil and gas producer leverages automation, they can make highly intelligent decisions through the technology features that enable enhanced monitoring, logic execution and visualization. They can also leverage these solutions to create a more secure operating environment and communications network. These solutions note only benefit the operators today, but they prepare them for future technology needs.
FreeWave Blog Series: The Intelligent Edge (Part 4)
The Internet of Things (IoT) has changed the consumer world in ways no one ever imagined. By placing intelligence in the IoT network, the “Thing” can do whatever we want it to do. Now Industrial companies are seeking to take advantage of this edge-deployed intelligence in order to maximize profits, improve safety and streamline operations. In addition to the challenges IoT technology had to overcome – such as cybersecurity, scalability and interoperability – Industrial IoT (IIoT) must also focus on reliability, ruggedness and more. FreeWave is uniquely positioned to understand and address all of these challenges. We have delivered world class IIoT platforms for almost 25 years to thousands of industrial and unmanned systems customers. With that experience, we’re now leading the charge to deploy intelligent applications at the edge of industrial networks and unmanned systems. In the fourth installment of “The Intelligent Edge,” we spoke with Helen Xi, a senior firmware engineer at FreeWave who specializes in high-speed wireless LAN performance, to talk about the use of broadband in the IIoT, as well as FreeWave’s industrial Wi-Fi platform, the WavePro. Read parts one, two and three. FreeWave: Can you talk a little bit about the WavePro platform and where it fits into what you work on at FreeWave? Helen Xi: In our company, the radios mostly operate in the narrowband frequencies, however WavePro is a broadband Wi-Fi system. It’s important for us to have this Wi-Fi system because nowadays there are so many Wi-Fi clients. It’s on every mobile phone, in every laptop, in every household. It’s everywhere. You can’t avoid it. When we have this Wi-Fi product, we can provide a whole communication system to customers. It’s easier for us to integrate them together to make sure they work from our Wi-Fi system to our narrowband radios. Our WavePro product has many features. If you compare it with the industry competitors, they have multiple products and models that meet customers’ specific needs. If you want to provide a long-distance point-to-point link and you buy this model, and you want their system to provide Wi-Fi local coverage, then you must buy another model. WavePro integrates all these features together in a single product, and we can do long-distance point-to-point link, local Wi-Fi coverage and mesh. It can have different clients while providing a backhaul communications in a remote area. FreeWave: Walking back a little bit on some of what you just talked about, one of the things that we’ve been discussing is the transition from traditional RF technology into technology that requires higher bandwidth to transmit bigger data packets in real time and run analytics at the Edge. With WavePro, what I’m wondering is when you talk to clients, what is their number-one priority with this technology? Are they trying to update existing systems or are they wanting to implement entirely new systems? And how important is the broadband aspect? Helen Xi: I think both. Let’s say they want to upgrade an older system. Let me give you an example: nowadays because there are so many Wi-Fi clients, Wi-Fi chips are so well-known, and more sensors have Wi-Fi client chips inside them. If we put our WavePro in the field, it can work as an access point (AP) to talk to these sensors. By the way, our product is an outdoor unit. It’s waterproof IP67. IP67 means you can immerse it underneath water. It has the same industrial-temperature range as our other narrowband radios. It goes from minus-40 up to 70 Celsius. It also has surge protectors from lightening. So, you can safely put it outdoors. If you buy a home Wi-Fi router, say from Netgear, you probably do not want to put it outside. FreeWave: And why is that element important? Helen Xi: Because a lot of our customers use it outdoors. For example, in North Dakota, it’s very cold. It can be minus-20 Celsius. I think you can imagine what happens to your iPhone during winter when you go skiing – it goes dead. Our radios don’t do that. You put it outdoors, on the oil-gas fields where it goes from winter to summer – as cold as North Dakota, as hot as Texas in the deserts – and it’s working well. That’s why the temperature requirement is important. FreeWave: When you’re talking about application examples, where else are you seeing this technology deployed? Helen Xi: It can be used in many areas of the Industrial IoT. For example, we have a utility company that uses WavePros to control large quantities of air conditioners on the roof of two apartment buildings. Each air conditioner has a 2.4GHz Wi-Fi chip in it. They all connect to WavePros on 2.4GHz. One WavePro (we call it “master”) is connected to the utility company’s network. The other three WavePros (we call “slave”) connect to the master WavePro on 5GHz. When the utility company needs to send command to air conditions, it first goes to the master WavePro; the master WavePro passes on its 5GHz to the other slave WavePros; then, the slave WavePros transmit on 2.4GHz to each air conditioner. FreeWave: What do you envision being the trend of the future with regard to Industrial IoT communications? Is it all headed toward broadband? Or do you think that there will still be a balance between that and cellular and RF? Helen Xi: This is a very good question. I believe it will be a combination. I want to elaborate why I think narrowband is still very important where people seem to only be talking about gigabits. Wireless as a resource is very valuable – every Hz (hertz) is valuable. When you are using a frequency band at this location at this instant, other people cannot use it. You are noise to other people. Plus, not every Hz is free to use. In IoT, we’re mostely using unlicensed band that you don’t need to pay a fee to the FCC to use as long as you follow rules. There are only
Calling Industrial IoT Developers…to the Well Pad?

Organizations continue to enhance their digital transformation strategies as they see measurable benefits and improvements in operations. Many industries that have traditionally used either manual methods or a disparate technologies for data collection, will soon have access to next generation, cloud-based monitoring and control of their networks. In these networks, robust wireless communication technologies bring intelligence to remote assets, enabling command, control and visibility from computers or mobile devices, and accessibility from anywhere. These future-proof wireless telemetry systems leverage automation and programmability to monitor data globally and execute and process logic locally. As organizations eye the future of operations with these types of capabilities there are big opportunities for software developers in the Industrial IoT (IIoT) space. Developers in Demand With programmability introduced to the industrial IoT network, the possibilities for developers are endless. Novice developers could even leverage open-source technologies like Python and Node-RED to enable new applications for monitoring and control that can transform business operations. We’re already seeing automation prototypes for tank level monitoring of remote and isolated oil/gas assets, and this is only one example of the type of application that would prove highly beneficial for organizations with geographically dispersed assets in the field. These programmable solutions are also extremely flexible, as a company can choose to develop the app themselves or integrate third-party applications. There is at least one pilot program currently in progress designed to support and enable developers who want to create applications for expansive IIoT networks. IIoT app development can serve a number of industries. The ability to add programmability to these solutions further supports companies as they digitize operations. Next Generation Automation for Oil and Gas Small-to-medium-sized oil and gas companies in particular can benefit from automation technologies that combine wireless telemetry with programmability, especially in terms of ROI. By automating manual processes, they cut down on operating costs by a large marker. Well pad automation technology builds analytics and intelligence into the wellhead environment. This is a big step beyond traditional communications because it enables the intelligent applications and programmability to establish an advanced operating environment. With a modern communication network in place, the organization becomes more agile and productive because it can leverage predictive analytics, remote command and control, new protocol translations, and modern cloud-based services – all at the well pad! When the oil and gas company has the power to make informed decisions that drive higher production outputs, they are able to visualize and measure the benefits. It’s an exciting time in the IIoT space as we watch digital transformations change the way companies operate. With more processes automated and programmability being incorporated throughout the entire network, even at the most remote edge, we’re seeing significant opportunities for developers to help point these industrial organizations at the future.
Programming for Cloud-to-Device Communications in Industrial IoT

Should you leave processing in the cloud or on the edge? Both. Particularly in IIoT, developers need to start thinking about both tracks. There is a power struggle going on in the Industrial Internet of Things (IIoT). Many think cloud applications are the future of real-time data processing in IIoT settings; others believe data should be processed and decisions executed at the edge of the network. In truth, the answer lies somewhere in the middle: Data needs to be processed both via the cloud and at the edge, which presents an interesting opportunity for software developers in the IIoT space. Clearly, being able to operate industrially hardened smart devices remotely – and in many cases automatically – from the cloud presents many benefits. But the challenge lies in potential connectivity issues when developing applications. Developers must think along a dual track, which means that they must think about how an app developed for the cloud can be mirrored to run on the edge device itself. Several factors converge here to create a unique atmosphere for developers: connectivity, security, and today, the programmability of edge devices. Traditionally, the devices themselves simply acted as conduits for data collection and transport, but today, hardware manufacturers are creating devices that can host third-party applications. A point worth noting is the advent of Node-RED, which can streamline some of the programmability challenges. So, understanding the need for mirrored applications, let’s look at a few use-cases that highlight exactly why this redundancy is necessary. Cloud-to-Device in the Oilfield In the case of oil fields, when the edge app sees an oil pump showing a temperature reading above a predetermined safety level, the applications on the device can decide to shut the pump down, or the cloud application can send a command to do so. In cases where there are emergencies, different sites might have a different set of actions that need to be initiated. In fact, most sites have thermal sensors on the oil pads. If the oil pads exceed a certain threshold, then these cloud programs know there is an explosion and a fire happening onsite. To prevent a chain reaction, the cloud will send a command to shut down all the pumps and all the valves in that area so they don’t create a chain reaction and keep spreading. Extending the oil site example, if there is an intentional attack on the site, the first thing you do is disconnect the communication lines back to the cloud to protect the network. In that scenario, having the same application running on the cloud and the edge devices still allows the same decision to be made in the local network by the device itself. If the device cannot ‘see’ the cloud, it can still respond and execute tasks. If the cloud program is not responding, and the device notices the pad temperature goes beyond the threshold, it can initiate a local shutdown protocol. Once the network is back online, the device can send this information back to the cloud which can, in turn, be given to site operators remotely. Because of these necessary duplications, programming for these settings can be difficult. For example, in Oracle applications, in SCADA networks, all of the applications run on Java. Oracle pages run on Java. Therefore, most programmable industrial devices must demonstrate that they can run the same Java application locally. Many IIoT platform providers have now expanded the scope of the programming. They’ve built devices that can actually drag and drop the same Java code from the cloud into individual edge units, to run that device. Of course, it has to be developed for a device and for the cloud, so it requires some extra attention, mainly because on the device, the decision-making is slightly different. It does not execute the application unless it cannot speak to the cloud. When it cannot speak to the cloud, then it executes the command just the way the cloud would. Redundancy Applications in UAS In other industrial settings – unmanned systems, for instance – the protocols are different. If a drone can’t communicate with the operator, it could have a simple command that says, “Trace back all your GPS location and fly them in a reverse mode and go back to where you came from, until you can establish communication and get new commands.” So, it’s the same concept. Programmable IIoT platforms are now being set up and designed so that they can run applications in multiple different languages. If the application is written in C, Java, Python – basically, anything that can be read on the cloud – it can be dragged and dropped into those edge units, and it could execute the same protocols directly on the edge device. This simple concept is transforming the way the IIoT thinks about data transport and real-time decision-making. If you write your code once you can drop it in both places, and if the device loses communication, it knows what to do. Of course, there are many other considerations when thinking about programming applications for the edge and the Industrial IoT. Security remains paramount, and we see examples every day pointing to a potential meltdown if security isn’t addressed properly. Still, the potential for the cloud-to-device communication and application execution remains great. For developers, being able to think across platforms, languages and program functions are three key points to consider when creating applications for the Industrial IoT. This article originally appeared on DZone.com
The Next Generation of IIoT: Micro & Macro Connectivity
From a consumer standpoint, the impact of IoT connectivity is clear. People can purchase smart home systems and automobiles with increasingly autonomous features. Looking at the potential changes to our daily lives in the coming years, all things point to connectivity. We are eyeing a future where we can monitor and control our homes, vehicles and business around the clock. The news stories are exciting and tangible because new products are frequently unveiled and we see them being used in our everyday lives. This impact has spread beyond the scope of the consumer market, which ultimately led to the Industrial Internet of Things (IIoT). Traditional businesses, like those in utilities, oil/gas and agriculture, face a future that has the potential to transform entire industries due to the power of digital disruption. Despite the growing pains and challenges of “going digital,” industrial businesses face almost limitless potential to streamline operations and control large distributed networks with a level of precision that was previously impossible. As these industries pick up on the value of data and connectivity, next generation applications have emerged that will drive competition and increase productivity. Data and analytics will be available via the cloud and accessible from any device. And even better, the quality of data will be controlled through automation and the incorporation of third party applications. What this means for businesses is they will be able to monitor their networks on a micro level. This allows problems to be stopped in their tracks and for precise process adjustments that streamline operations. With third party applications, there is not only substantial business opportunity for developers, but there are endless possibilities for process control, security and operational apps that will drive down costs and support increased production. Most business decision makers are aware that there is no stopping digital transformation because research shows that it’s already happening. Many businesses are in the process of digital transformation and have already thought about these next generation systems and the research proves this: 75 percent of IoT providers say that big data and analytics are among the top skills they look for when adding talent to their teams. 50 percent of companies look to hire specialists in mobile development. A recent TechBullion article states: “they already have noticed the close relationship of mobile and IoT and plan to launch IoT projects for their businesses within the nearest 5 years.” Gartner says that by the end of 2017 demand mobile application development will grow five times faster than the number of IT companies able to meet this demand. A new report from Frost & Sullivan anticipates a trend in the transition from connected devices to the use of cognitive or predictive computing and sentient tools in the next 12-18 months. So what does this mean for industrial business? It means they need to invest now in the communication technologies that will deliver the data that is absolutely critical for future networking needs. It means they need to think about how they can enable programmability at all network endpoints – even at the edge. And lastly, it means they need to start working through the challenges of a digital shift now so they are prepared for an automated, connected future.