Your Employees are Talking, But Are You Listening?
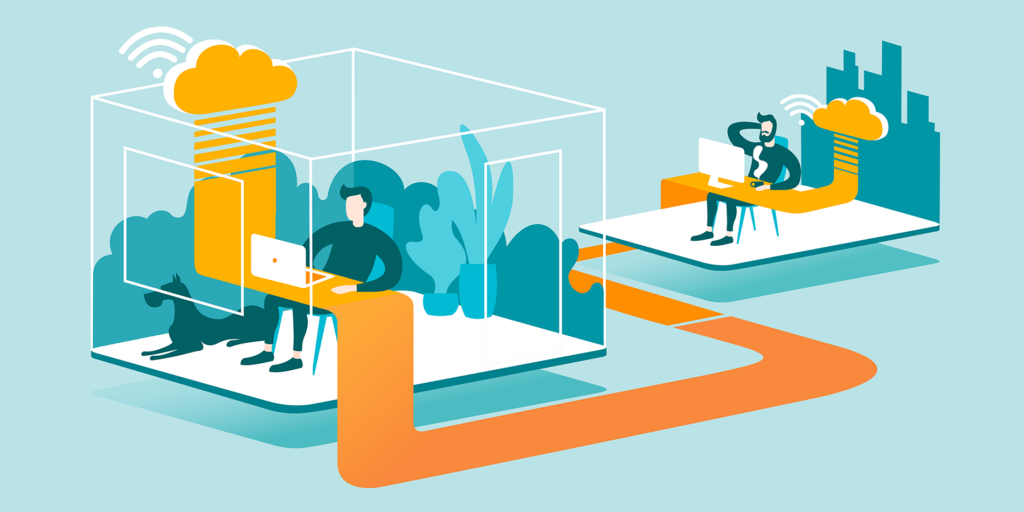
FreeWave’s Kirk Byles explains why listening to your employees is an easy way to increase engagement and productivity among remote teams. WIRED recently published an article about why we are seeing pushback from executives about working from home despite the fact that businesses have transitioned successfully to the WFH model and employees routinely express greater satisfaction with it. The article highlights the disconnect in both planning and execution between executives and staff and it basically comes down to three things: assumption, bias, and transparency. It’s not about knowing all the answers, it’s about asking the right questions. One of the most important things we’ve done at FreeWave during the pandemic when working from home wasn’t a choice, but a necessity: increase the cadence of our engagement survey to every six months and *really* listen to feedback. Like most businesses in the last two years, we had to react quickly to the changing tides of COVID. We shut down our office on March 13th of 2020 and, after consistently receiving meaningful and reliable feedback from our staff, we decided to transition to a “remote encouraged” culture. And, it’s working. The article mentions that executives have very differing views, experiences, and appreciation for in-office than most of their own staff. There are assumptions and biases about what is needed for both productivity and engagement and about the experience that most staff have versus the experience of the executive. The survey refers to it as “a focus group of one. I have X, Y, and Z resources and experience so that must be true of everyone in the company from Assembler to Customer Service and Accounting.” We approached the challenge of engagement with a simple premise: we don’t know the answer so let’s ask questions and base an iterative plan on the data. We wouldn’t start developing a product without market research so why would we do the same with employee engagement? Transparency and the Fail Fast Philosophy In the article, Brian Elliott of Future Forum cites the reticence of executives to announce an action plan if they “don’t know all the answers”. Maybe it’s because we’re a tech-based business where iteration is the norm or maybe COVID taught us lessons in adaptability but, whatever the case, we’ve always understood the fail-fast philosophy is not just for the technical side of the company. While actively addressing the issues of assumption and bias in collecting the survey data, we still had one more challenge to address and that was transparency. To that end, not only do we present ALL survey data in our quarterly All Hands; we also announce specific plans to address areas of concern. We set expectations and not only encourage employees to hold us accountable for the action items but acknowledge that these plans build upon each other. In every, all-hands gathering we summarize any changes in survey results, announce whether the previous two- quarters plans’ have seen any success, and move forward with new plans to either maintain or improve engagement results. These relatively short timelines and repeated testing allow us to move quickly to actively address not just employee needs but the needs of the business as a whole. Results As any businessperson knows all it takes for top talent to leave is a phone call from a recruiter on the right day. Businesses who have neglected to both survey their employees, publicly announce results, and work on improving engagement are seeing this in droves. I’m sure there are many other companies like FreeWave that don’t have the ability to provide many of the perks that other large tech companies rely on such as gyms on-site or free food or even salaries in the top 10%. However, on the flip side, many of those companies have doubled down on returning to the office and implemented micromanagement and monitoring tools of their staff and even old-fashioned dress codes and attendance policies. Their employees become more frustrated at losing the flexibility, trust, and better work/life balance benefits they have come to appreciate during the pandemic. If they were successful and thriving over the past 18 months, why should we consider they wouldn’t be going forward? Maybe we’re lucky, but we’ve been able to attract some really top-tier talent from larger organizations by providing, not just the flexibility employees’ demand, but the trust that allows them to flourish.
Smart Farmers Use Data, Do You?
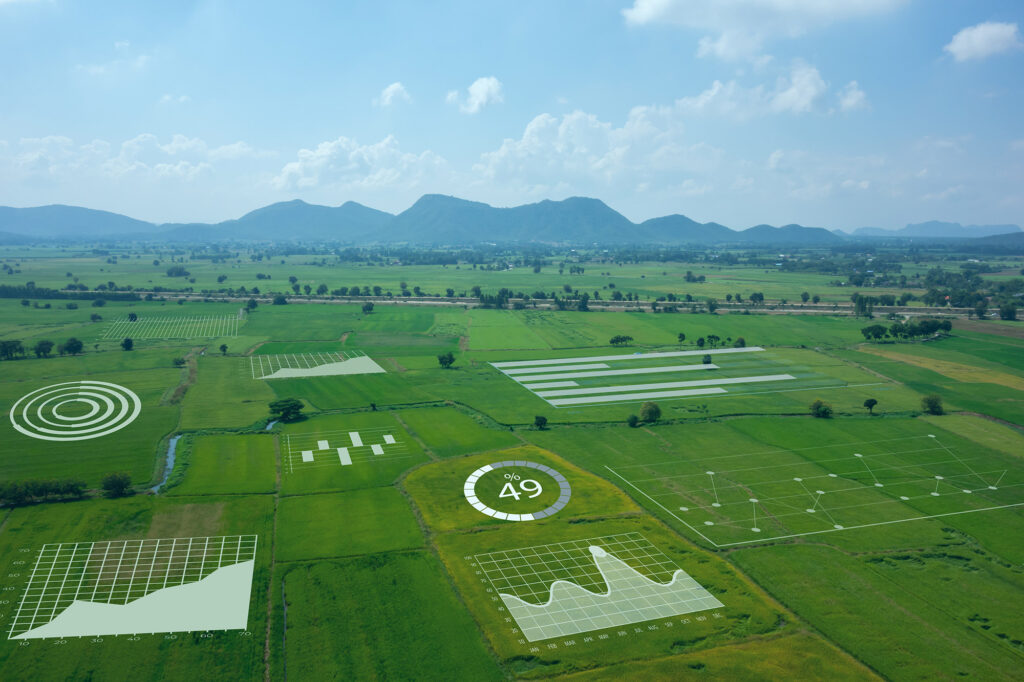
Data has revolutionized the planting, growing, and harvesting of crops on farms worldwide. Here’s why intelligent farmers use data to drive decisions and boost profits. Data, not unlike the introduction of the cotton gin during the Industrial Revolution, is rapidly changing the way farmers make decisions and operate their businesses. It’s not just to save energy or boost profit margins, either. Based on predictions that the population will reach 9.7 billion people by 2050, experts at all levels are looking closely at sustainable ways to increase healthy food production. Tech tools that rely on data are typically the cornerstone of these initiatives. But how do farmers use data exactly? And why is it wise to adopt tech into the harvest cycle? Keep reading to find out. What is data collection in agriculture? Data collection in agriculture is one of the foundational components of smart farming (also called precision agriculture). Relying on technology to gather information throughout the agriculture lifecycle, farmers can narrow the scope of their farming practices and optimize their processes. Examples of data collection in agriculture include: Crop yield data Soil moisture level monitoring Drone or satellite imagery Streamlining and enhancing farming practices Optimal harvest time Why is data critical in agriculture? As the population increases globally, experts look closely at how the agricultural industry can increase healthy food production while remaining sustainable and profitable. Using data to drive decisions and monitor operations helps farmers achieve both goals. How can the IIoT be used in agriculture? IIoT (Industrial Internet of Things) is a term used for the billions of devices worldwide now connected to the Internet. IIoT and automation in agriculture are closely linked to precision agriculture and data collection on farms. Data is typically collected via IIoT-connected sensors and tools that compile, sort, and analyze the information. These devices do more than just offer suggestions, too. Many are autonomous, which frees up farm owners to focus on the big picture of their operation. How are data and analytics transforming agriculture? Here are some ways data is revolutionizing how we plant, grow, and harvest healthy food. Off-Site Crop Production Data From the time seeds are planted to when the optimal time comes to pick a fruit or vegetable, data is changing how—and where—farmers work. Farmers no longer have to be on-site to make critical decisions. Instead, using a computer or even a smartphone, they can execute decisions from home. Healthier Soils Using drones and other imagery technologies, sensors determine soil moisture levels and overall health from the air. This not only improves the quality of the end product but makes farming more sustainable too. Soil erosion is a considerable worry in the eyes of environmentalists, who say monocropping is responsible for soil erosion in America. For example, topsoil levels in Iowa have shrunk by as much as 50 percent in Iowa, one of America’s biggest producers of corn, soybeans, and oats. One solution to this is to regularly rotate plantation sites, which data collection can help identify. Strengthened Supply Chains Food waste at the farm level is an oft-overlooked issue. Many believe waste only happens at the grocery store or once consumers take produce home with them. But one study found that as much as 30 percent of food never leaves the farm and is simply left there to decompose. Increased supplier and shipping costs and blemishes or imperfections on produce are two reasons this happens with alarming regularity. Collecting data helps farmers harvest at the optimal time and identify outlier products early in the growth cycle, making their practices more efficient. Is IIot the future of agriculture? Yes, assuming you don’t already consider IIoT the “present” of agriculture, too. Tech experts believe the IIoT will bring farming practices to the next level, making them streamlined. For example, crop-picking robots that determine ripeness and readiness of produce are becoming a regular thing on farms across America. As price points for these devices decrease, they will likely become ubiquitous. The IIoT plays an integral role in getting crops to the point that they’re ready for robots to harvest them. And as more robots, drones, and sensors are placed on farms worldwide, more data will be available to farmers to make critical decisions that lead to more products using fewer resources. What are the limitations of agriculture data systems? One of the significant limitations of agricultural data systems is a lack of connectivity in remote areas. Collecting data is essential, but if farmers can’t access the information in real-time, the data is less effective and may still lead to delays or costly errors during the growth cycle. Fortunately, FreeWave’s agricultural solutions can solve connectivity issues in the harshest and most remote environments, so farmers never have to worry about accessing their data in real-time. Infuse intelligence into your agricultural operations today with FreeWave. Click here to learn more.
Five Ways to Improve Agricultural Efficiency With IIoT
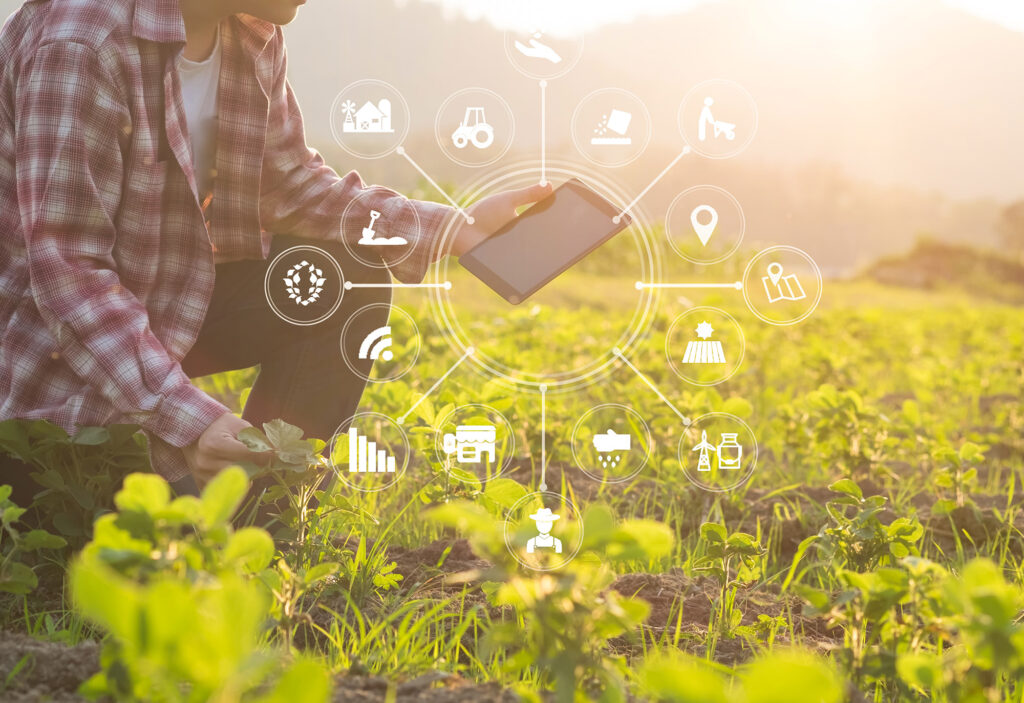
The IIoT benefits farmers and their products substantially, especially regarding how efficient growth cycles can become. Learn more in this article. It’s estimated today that half of the organizations in the agriculture sector have adopted IIoT capabilities, according to Inmarsat Research. Even those who have yet to buy-in, largely agree that the Industrial Internet of Things (IIoT) is quickly revolutionizing how farmers grow food and people gain access to healthy food on a global scale. Increased efficiency is one of the main benefits causing farmers to switch to tech-enabled smart agriculture. Below, learn why smart agriculture is quickly becoming ubiquitous, as well as five ways these tools can optimize crop yields, increase profits, and simplify the farming process end-to-end. What Is Smart Agriculture in IIoT? Smart agriculture as it pertains to the Industrial Internet of Things (IoT) is the process of fine-tuning and optimizing the product cycle using digital tools. These devices work synchronously to gather data and deliver critical insights that can be carried out by the technology itself or at the farmer’s discretion. What are the Various IIoT Tools for Agriculture? IIoT agricultural tools include, but aren’t limited to: Crop management devices that collect data such as precipitation levels, temperature, and soil quality. Agricultural drones that determine soil health from up above distribute localized pesticides and more. Cattle health monitoring and management devices. Greenhouse automation systems. End-to-end farm management systems. How does IIoT Impact Our Lives Through Agriculture Automation? It provides larger quantities of natural food for a growing population. It lowers farmer production costs, which passes on savings to consumers. It increases product standards, creating healthier food at lower price points. It keeps workers safe and allows them to work efficiently. It enables farmers to grow their business safely and effectively, with far less risk than previous years. How to Use IIoT in Agriculture to Improve Efficiency (5 Ways) Here are five ways the Industrial Internet of Things can be deployed in agriculture to improve efficiency. 1. Monitor Climate Conditions The use of sensors is one of the keys to well-executed precision farming (or precision agriculture), which is the art and science of making accurate decisions based on data. Often, climate sensors are the first piece of IIoT tech implemented in an agriculture setting. These devices monitor climate conditions, soil quality, pesticide output, and other vital levels to help farmers increase yield using fewer resources. 2. Implement Tools that Reduce Production Risk One of the significant advantages of IIoT in farming is the early identification of issues that could otherwise be missed or overlooked due to human error. This lowers production risk and gives farmers a better idea of what their harvest will look like months in advance. Lower production risk gives farmers better control over product distribution, ensuring they acquire buyers early enough in the season and don’t wind up with unsold products. 3. Use IIoT Agriculture Tools that Lower Cost and Reduced Waste IIoT capabilities reduce operational costs for farms of all sizes. More accurate data boost output without increasing staffing—and healthier, more robust crops yield better profit margins, too. According to Inmarsat, lower operating costs have created a more sustainable farming practice for 37 percent of farmers. 4. Use Technology to Elevate Crop Standards With a firm grasp of the production process and more data to conclude from, farmers can use IIoT devices to produce healthier, nutrient-dense food. A higher standard yields better profits, as well as reputation and growth capacity. This is true for the product of fruits, vegetables, and even cattle. Whatever the product, intelligent agricultural tools help farmers identify outliers, address localized issues such as pest infestations, and deliver those signals (or an appropriate intervention) before it’s too late. 5. Use Mobile Devices That Allow for Flexible Work Gone are the days where farmers had to be on-site throughout the entire grow cycle to ensure the health of their products. Thanks to mobile devices that utilize edge solution technologies, farmers can access information remotely from a smartphone or application. Because many devices work autonomously, the number of decisions farmers must make in general has also been drastically reduced with IIoT technology. What are the Challenges of IIoT In Agriculture? As it stands, the significant challenges of IIoT in agriculture relate to robust internet connectivity in rural areas and elevated hardware costs. Fortunately, though, affordable solutions like ours use rugged hardware and even satellites to provide farms with the power they need to stay connected. The growth of IIoT tech in agriculture (and all sectors) is all but inevitable in the coming years, though. So these current challenges may become nonissues faster than many would expect. Visit our site to learn more about FreeWave’s Smart Ag solutions: https://www.freewave.com/industries-applications/precision-agriculture/.
A Starter’s Guide to IIoT and the Fourth Industrial Revolution (aka Industry 4.0)
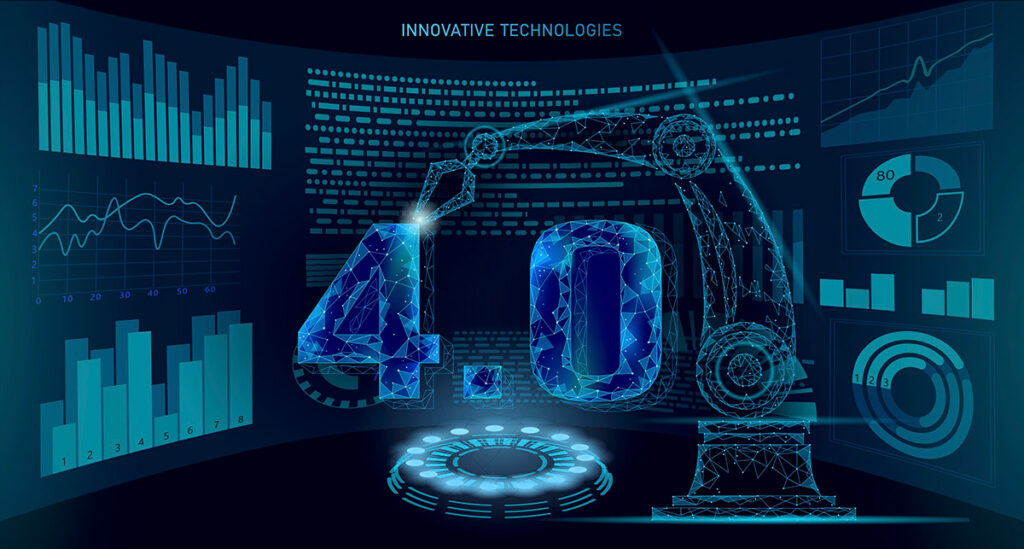
Industry 4.0 is revolutionizing how businesses operate and manufacture products. In this guide, learn how the IIoT plays a considerable role in this movement. The Fourth Industrial Revolution, or Industry 4.0, is a term many use to describe the new way products are created and sold thanks to technology, specifically the Industrial Internet of Things (IIoT). Depending on who you ask, we’re right on the cusp of Industry 4.0—or smack dab in the middle of it. While there’s no set definition (the term was originally used for a German initiative in 2011 and has significantly evolved), manufacturers still need to understand how the Fourth Industrial Revolution could impact their business. This starter’s guide will help you understand the critical points about IIoT and Industry 4.0. What Is the Fourth Industrial Revolution? The fourth industrial revolution, or Industry 4.0, is an evolution of manufacturing that enables automation. In short, it’s the marriage of physical production with intelligent technologies. Industry 4.0 builds off the back of industry 3.0 (which began in the 1970s). As a refresher, here are some of the manufacturing advantages that came out of each of the previous Industrial Revolutions: Industry 1.0– mechanization, the introduction of steam and water power Industry 2.0– electrical power that enabled mass production Industry 3.0– tech and electronics make mass production easier, increase efficiency Think of Industry 4.0 as relying more heavily on technology to take manufacturing to the next level. No longer is tech being used in conjunction with people but as the focal point of the operation. The IIoT and Industry 4.0 The industrial internet of things (IIoT) refers to the network of billions of devices (literally) equipped with sensors, monitoring devices, and other technologies that power applications and drive decision-making in industrial settings. Connected capabilities and real-time feedback through sensors are considered major elements of the Industry 4.0 movement. Examples of the IIoT being a part of Industry 4.0 include: The automotive industry relying on industrial robots for manufacturing The oil and gas industry using remote sensors to identify pipeline problems The agriculture industry using industrial monitoring devices to check soil levels and improve yields with harvest automation Even utilities like water and electricity benefit from the IIoT’s capabilities. (For example: see how FreeWave’s capabilities brought 50 percent savings to Sangamon Valley Public Water District in Illinois.) Occasionally, you may find an “IIoT vs. Industry 4.0” debate online, but it isn’t an either-or discussion. The IIoT is a major strategic component of the greater Industry 4.0 movement. The two terms are sometimes confused because they both focus heavily on improving manufacturing processes. Benefits of the IIoT in the Industry 4.0 Movement Adopting technologies that fall under the Industry 4.0 umbrella can be quite valuable for a business. Tangible benefits include: Improved productivity and efficiency Lower operating costs Simpler compliance procedures Improved safety in work environments, especially in dangerous work settings Adopting an Industry 4.0 model also allows leaders to innovate in their field and potentially move ahead of the competition. Below are two specific examples of how the IIoT can improve a business’s operational efficiency and boost its bottom line. Edge Computing IIoT edge computing gives time-sensitive operations predictable, safe analysis from a remote location without a central network system. For example, in the case of an offshore oil rig, a loss of signal could result in expensive repair costs or even security threats. Edge computing uses low-power devices to send vast amounts of data, allowing employees to make decisions from a safe, remote location. Machine Learning, AI, and Predictive Technologies Big data poses endless opportunities for improvements in the manufacturing process. For example, it can improve supply chain management and enable the personalization of products without increasing costs. The problem is, data needs to be organized and usable. Tools like machine learning and AI can sift through and collect data for business leaders and make highly accurate decisions using predictive technologies. What’s Next for the IIoT and Industry 4.0? As it stands, the future of Industry 4.0 is pretty easy to sum up: those who make the switch stand to make significant savings and increase efficiency. Those who don’t adopt Industry 4.0 models risk facing substantial hurdles, especially related to operating costs. When your competition starts using the Industry 4.0 model and can produce a better and faster product for less, that could spell trouble. Most estimates show the IIoT will grow by billions of devices each year for at least the next five years. Of course, each industry will be affected a little differently based on how quickly they adopt the principles of Industry 4.0. Still, the consensus is that this massive network of tiny devices is here to stay—and therefore should be considered carefully by business leaders.
15 Benefits of Embracing IIoT and Automation for Manufacturing
The Industrial Internet of Things helps leaders thrive in crowded and even dangerous markets. Here are 15 benefits of embracing IIoT for manufacturing. Embracing the Industrial Internet of Things (IIoT) for manufacturing is one way to win in highly competitive or dangerous markets. Automating production and relying on high-tech sensors to give you crucial feedback not only benefits your bottom line but it also benefits those who work for you. Here are 15 benefits of embracing IIoT and automation for manufacturing. 1. Cost Savings IIoT connectivity reduces manufacturing operation costs by: Reducing on-site staff requirements needed for measurements Reducing energy costs Reducing maintenance costs Improving system efficiencies and eliminating bottlenecks Identifying bottlenecks and problems Making any switch can feel uncomfortable for a business, but your bottom line stands to improve from the decision to embrace IIoT for manufacturing. 2. Continuous Monitoring Billions of dollars are lost each year due to downtime, errors, and faulty production in manufacturing. Fortunately, IIoT technology offers continuous monitoring, which alerts you the moment something goes awry. This is another way to save money and reduce the potential for on-site injuries. 3. More Efficient Systems IIoT computing systems move data to the edge, freeing up your on-site devices to collect more information with less power. The future of IIoT and edge computing is even brighter, as more real-time data will be available for extraction, and data will be easier to customize. 4. Improved Production Flow Communication is the key to streamlined production, and it’s simply a fact that computers equipped with high-grade sensors communicate better (and more efficiently) than people. Every aspect of production stands to improve with IIoT making real-time decisions. 5. Mobility Each IIoT item offers a virtual component (along with security features to protect your data). Experts expect that over 50 billion devices will be connected by 2022, which gives your company the ability to do more with its data and mobility by embracing IIoT for manufacturing. 6. Predictive Technologies Newer IIoT connectivity tools come with sensors and wireless transmission capabilities that draw vital conclusions about your manufacturing processes. The longer they run, the more refined their analyses become, identifying more minor bottlenecks and streamlining processes of which you’re probably not aware. 7. Personalization As the Industrial Internet of Things grows, the possibilities for personalization will too. For example, you can customize aspects of your inventory and supply chain management to help your business run smoother. 8. Improved Safety IoT allows manufacturing employees to be off-site while they work. It also ensures continuity in the event of disaster or disruption. This is especially helpful for industries where manufacturing may be dangerous (steel, certain foods, etc.). 9. Improved Customer Service In business, giving customers what they want at the right price is critical. Intelligent devices that automate your work and derive key insights to improve efficiency help you narrow down what you do, do it faster, and perform the job at a higher quality for your customers. 10. More Business Opportunities IIoT frees up time on the manufacturing floor to expand the business. It also allows manufacturers to create new products and pivot or include new services for existing customers to promote retention. 11. Thrives In Competitive Industries The larger and more competitive the industry, the stronger IIoT becomes. For example, IIoT tools in oil and gas free up data to provide critical insights at drilling sites without employee monitoring. Manufacturers can use this data to improve yields, prevent injuries, and lower operational costs, which could save hundreds of millions of dollars. 12. Cut Out Processing Time Manufacturers used to send all their information to a central location for processing. Today, though, the IIoT skips this step altogether without tearing down your network. Amazingly, it also doesn’t require you to replace existing infrastructure. Believe it or not, FreeWave’s industrial manufacturing IIoT solutions can reduce existing bandwidth up to 95% with no drop-offs in quality or transmission time. 13. Ensures Compliance OSHA violations can cripple a manufacturing business. The IIoT promotes a safer environment that helps you stay OSHA-compliant no matter the industry. 14. Improved Maintenance Scheduling Human error is a common factor that leads to serious manufacturing problems. For example, inconsistent or lax maintenance schedules could lead to expensive repairs or injuries. IIoT automation takes this off your business’s plate entirely. 15. Marketability Today, many customers understand the benefits of IIoT and seek it out when shopping for manufacturers. This is one reason experts expect IIoT in manufacturing to surpass $1 billion by 2026 globally. Manufacturers can stay ahead of their competition and even grow their business by offering better and faster data. Are you ready to take the next step in your manufacturing operations with IIoT? FreeWave wants to help. Get in touch with us today.
Automation in Oil and Gas: A Starter’s Guide
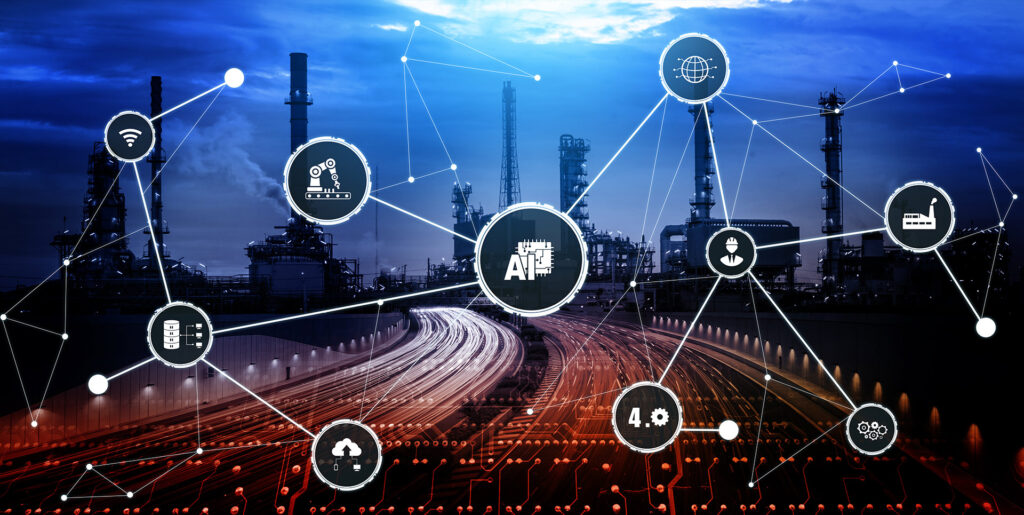
From drilling to logistics to preventing theft, automation in oil and gas is quickly becoming the standard. Learn how tech helps increase ROI and improves safety in this starter guide. Since the 1990s, businesses have looked at how automation in oil and gas can improve worker safety, improve efficiency, and increase the bottom line. Today, digital tools are being used in every facet of oil and gas cultivation. From improved efficiency when drilling for new oil to real-time weather monitoring and theft prevention, tech tools are quickly becoming the norm for the $2.1 trillion (according to IBISWorld) industry. In this starter guide, you’ll learn how innovation and automation in oil and gas is being used to connect, collect and analyze data, and increase ROI. What Is Automation In Oil and Gas? Oil and gas automation refers to the growing number of digital techniques and processes used to help producers cultivate energy. Automation and agility have found their way into nearly all oil and gas industry divisions, like drilling, logistics, supply chain, and safety. Tools such as rugged wireless radios and AI-powered real-time sensors for remote monitoring allow drilling sites to be run safely and efficiently from afar—protecting employees and increasing revenue simultaneously. Benefits Improved production yield while lowering costs Improved safety for employees in hazardous conditions Real-time insights 24/7 monitoring Theft protection at drill sites and along pipelines Sustainability Predictive technologies can be used for future application Where Does Automation In Oil and Gas Happen? Approximately 94 billion barrels of oil are produced every day worldwide, according to U.S. Energy Information. Here are some specific examples of how automation impacts the production and monitoring of two of the world’s most important resources. Drilling Autonomous drilling control systems (ADCs), such as those implemented in the North Sea (between England and Scotland) in 2020, enable safe and efficient oil drilling. In the past, “automatic” tools used to drill for oil were just manually assisted. Today, though, ADCs are believed to reduce drilling costs by as much as 50 percent. Diagnostics In an industry where downtime can severely disrupt a business and lead to financial downfall, remote diagnostics help predict future issues or pinpoint current ones to prevent delays and disruptions. For example, tools that measure pressure loss, temperature, and mercury levels can help businesses disrupt downtime and minimize costly delays. They also reduce the risk of oil rig disasters, such as the infamous Gulf of Mexico explosion on the Deepwater Horizon oil rig that left 41 miles of oil in the ocean. Weather Monitoring Oil and gas production are both contingent on weather patterns. Issues that can affect (or even shut down) drilling sites include: Tropical cyclones (most common) Extreme cold Extreme heat Earthquakes Automation in gas and oil includes the adoption of real-time sensors and monitoring tools, which detect changes in seismic activities and atmospheric levels, giving companies the ability to adjust in real-time to changing weather patterns. Security Theft in oil and gas is a real threat. In fact, a 2021 report said that Nigeria loses an average of 200,000 oil barrels per day (b/d) to theft, primarily from pipeline sabotage. Rugged, wireless radios allow oil and gas professionals to communicate safely without fear of interception or lost connection. Along with real-time monitoring of sites and pipelines, this can create a formidable defense against criminals. Trends in Oil and Gas Automation Oil and gas automation is quickly becoming standard, and with it, innovation in the field is coming. A significant push towards sustainability. Tech tools that help reduce a business’s carbon footprint and improve operating efficiency will be both sought after (and possibly required) in the coming years. Greater use of AI at oil rigs. Businesses are shifting away from manually assisted technologies in favor of artificial intelligence devices that make real-time, autonomous decisions on-site. More tech jobs. As on-site employees are phased out to make for a safer work environment, new jobs, such as coding, system architecture, and cybersecurity, will be created in the oil and gas industry. Contact FreeWave to learn how our technologies can boost your oil and gas business’s ROI today.
Increasing Healthy Food Access and Improving Yields With Harvest Automation
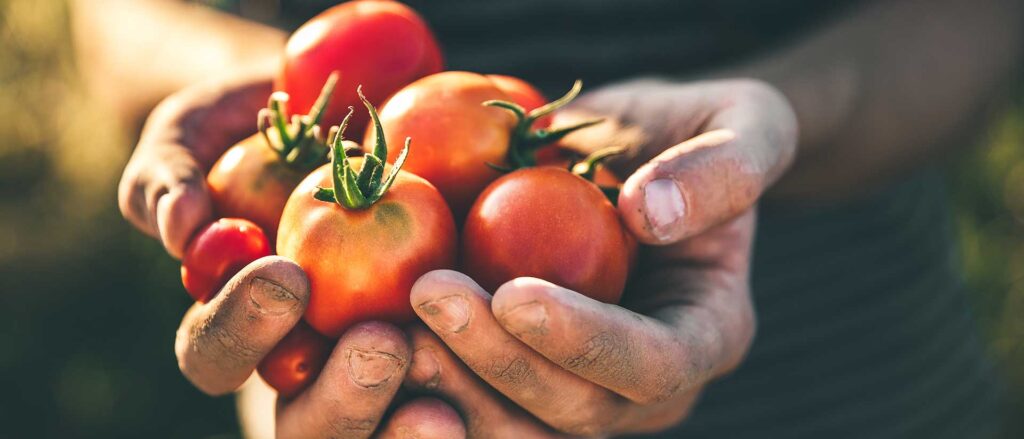
Increasing Healthy Food Access and Improving Yields With Harvest Automation What is automation in agriculture, and how are farmers using robots and other technologies to streamline food production? Our guide explains it all. From farm to table, technology in agriculture is quickly becoming an essential part of how Americans access healthy food. Experts anticipate explosive population growth in the coming years, and we expect agricultural automation to increase with it. But how exactly are farmers using harvest automation? And how are they using robots and drones to grow crops safely and cost-efficiently? Here’s an introductory guide to the state of automation in farming today: What Is Automation In Agriculture? Automation in agriculture relies on technology to streamline and optimize the process of food production in traditional farming. From drilling to planting to harvesting crops, automated farming technology is becoming more prevalent at all levels of the growing process. In 2017, TechCrunch estimated that $1.7 billion had been invested in automation farming technologies, a considerable increase from just a decade earlier. How Can Farming Be Automated? Automated farming tools aren’t only used for harvesting crops. Here are just a few examples of how technology is utilized throughout a season: Robotics are deployed to seed and weed areas of a farm. Computer sensors help identify problem areas, which reduces large-scale pesticide use in areas that don’t need it. Drones monitor weather conditions, assess soil states, and even render decisions without contacting the farmer. Beyond the farm and into the warehouse, forklifts are being replaced by automated guided vehicles (AGVs), which can load and unload food trucks, transport items across warehouses, and operate in cold storage climates for longer than human workers can. How Has Automation Affected Agriculture? Automation relies on remote sensors and other tools to more efficiently grow, monitor, and harvest crops. Using the Industrial Internet of Things (IIoT), the farmer makes real-time judgment calls unnecessary. Drones and robotic devices can collect data and interact with other computer systems and make critical decisions. For example, tech tools that determine soil moisture levels and seed population are being utilized more frequently. Farmers rely on absolute precision to grow their crops. As automation tools become more adept at maneuvering through agricultural challenges (weather patterns, for example), there’s a strong possibility it will become the go-to way to produce food. Is Automation In Agriculture a Good Thing? There are many advantages to automated farming, many of which are related to the ever-growing population of humans on earth and their need for accessible, healthy foods. The UN expects the world’s population to grow by 2 billion people between now and 2050. With a world population of just under 10 billion, it’s more important than ever to think critically about how the farming industry can adapt to the growing number of hungry mouths to feed. Here are some of the advantages and drawbacks of farming automation. Advantages of Agricultural Robots Lower labor costs (improves yields in less time) Provides more food at affordable costs to consumers A potential solution for growing population concerns Trustworthy technology simplifies the job a farmer has to do Enables farmers to hire less staff, giving them wider profit margins Less human error Drawbacks of Agriculture Robots Initial technology investment costs can be steep Potential trust issues with evolving technologies Maintenance costs High energy requirements The Future of Harvest Automation With a more than 30-year decline in the farming job industry and an apparent need for large-scale food development solutions, it’s pretty clear that harvest automation is here to stay. The recent COVID-19 pandemic has forced many American industries to take a hard look at artificial intelligence devices for food production. Going forward, more precise tools will emerge that make a farmer’s job easier and more profitable. Artificial intelligence will continue to improve, and both consumers and landowners will benefit from the round-the-clock abilities of field technology that no farmhand can match. Check out how our Industrial IoT Edge Platform can transform your operations today.
IIoT For Electric Utilities: The Past, Present, and Future
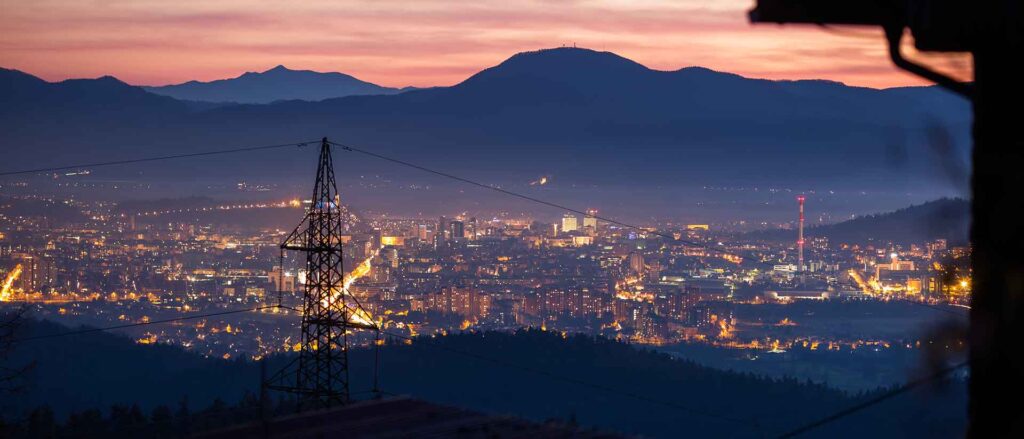
Electric companies are poised to become future IIoT leaders. Here’s why. Primarily driven by Advanced Metering Infrastructure (AMI), the Industrial Internet of Things (IIoT) has fundamentally changed electric utilities. Technologies that let devices act as two-way communicators between consumers and utility providers paved the way for new opportunities. Digital transformation is here, and businesses have to reinvent themselves to stay competitive and relevant. Still, many electric utility providers aren’t ready to leap into Industrial 4.0. Why? Because adopting and integrating smart tech into legacy IT and OT infrastructures can seem daunting. Learning new skills is challenging and takes time, and potential setbacks, like unplanned downtime, can leave utility leaders fearful. Many utility leaders are riddled with doubts regarding the technological uncertainties of IIoT. It’s understandable. With rapid growth come growing pains. The IIoT journey from uncomplicated AMI to vast, smart grid expansions is challenging. Urbanization is quickly expanding, energy prices constantly fluctuate, legislation is always changing, and sustainability is paramount. Because of this, utilities must refine their operations to meet evolving consumer demands for sustainable, affordable infrastructures. IIoT adoption won’t happen overnight, but you have to start somewhere. Here’s how: Introduce real-time monitoring equipment like sensors, readers, and alarms into your operations. And use technology to automate processes, conserve resources, improve outcomes, and eliminate downtime. Still, understanding how IIoT can impact your business is a great place to start. How can IIoT solve your problems? The benefits of IIoT are hard to ignore. Almost no one would balk at real-time data collection or say “no” to monitoring critical system health. Who would pass on the opportunity to improve efficiency and safety? Almost no one. Let’s face it. Competition is stiff, and unhappy customers create churn. Cost and efficiency drive consumers these days. They’ll switch providers with a simple click. Customer churn is inevitable if you can’t provide reliable service. That’s why your technologies must allow you to react in real-time. Seconds count when it comes to your customers. Connecting your devices, sensors, and alarms to the Internet, lets you monitor and utilize data in real-time to: Increase efficiency Use automation Reduce errors Work remotely Enhance security Boost profits Make better decisions These are benefits you can’t afford to miss. Implementing IIoT is a surefire way to open personalized customer communication. IIoT lets you tailor services to specific customer demands. We can’t understate the value of using edge technology and wireless connectivity to remotely operate, analyze, and optimize your electric utility operations. As energycentral.com points out, “utilities who refuse to adapt or change will suffer financial losses, countless preventable maintenance issues, and a waste of resources.” How can utilities lead the next wave of IIoT? IIoT is how power and utility providers will operate in the future (many already are). Traditional energy production and distribution methods are obsolete, and the days of manual processes and zero real-time visibility are over. IIoT is transforming how utilities run vast, widespread, and remote operations, and internet-connected devices and machines are reshaping the ways utilities operate. Technology never stops evolving, and transitioning into Industrial 4.0 and IIoT isn’t an option anymore. The pandemic increased automation and digitization demands, producing a ripple effect that’ll extend into the future of IIoT. Utility companies are partnering with tech companies to create innovative solutions to improve sustainability and become more efficient. As IIoT adoption accelerates, the opportunities to provide amazing service increase exponentially. With IIoT, utilities are proactive instead of reactive. And predictive maintenance through AI lets utilities continually learn and optimize operations. It’s a new era in the power industry. And smaller utilities are outpacing massive corporations. Smaller, more agile businesses are transforming the industry with their smart business models. And these same small businesses pose a threat to established corporations digitally transforming too slow. Providers that embrace IIoT will emerge as utility leaders in the next several years. Put your business and your customers first. You can’t afford to not implement IIoT into your electric utility operations. It’s time to put your business and your customers first FreeWave is second to none when it comes to proven IIoT solutions and making the most of your data. We’re the leaders in edge computing and wireless connectivity. We’ll accelerate your digital transformation. Our technologies are fast, flexible, and easy to deploy. We’ll have you leveraging IIoT, big data analytics, and connectivity to take the guesswork out of your operations in no time. And you can do it all without a complete infrastructure overhaul. You’ve been improving your utility operations for years; why stop now? We want to take your operations to the next level. Get in touch; let’s chat.
What Does the Future Hold for IIoT, Automation, and Edge Computing?
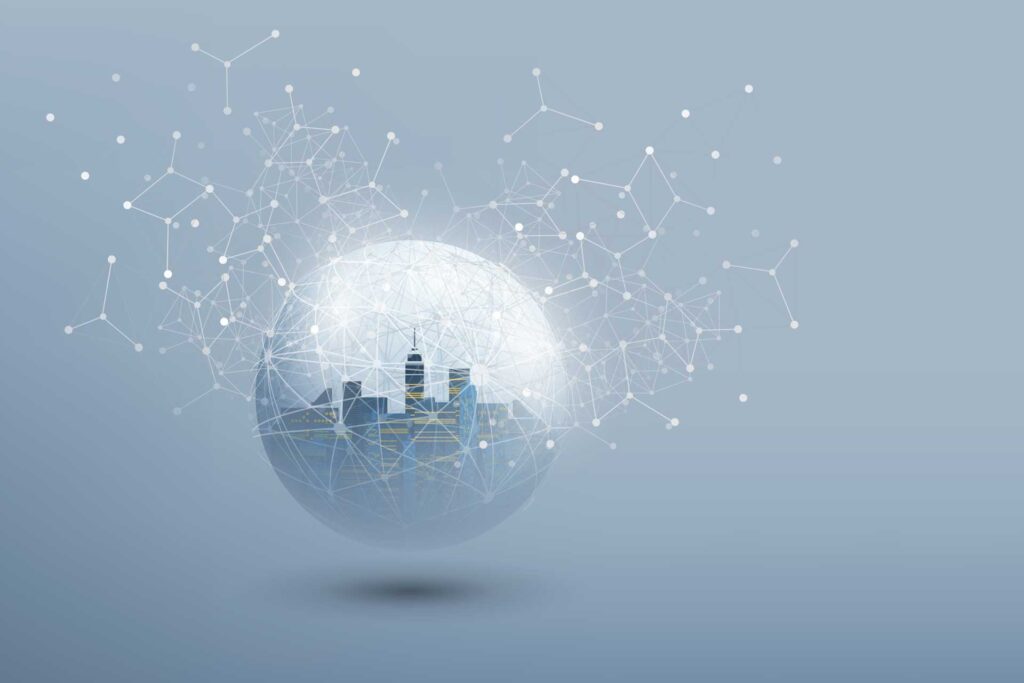
From narrowband communications to edge computing, FreeWave continues to solve significant customer challenges with IIoT, automation, and data collection. We are excited about our 2021 product roadmap. We are making a significant leap forward into Edge Computing. This quarter, we will be releasing two new products: FreeWave Edge and FreeWave Fusion Bridge. Before we look at these new solutions and where we are heading,I’d like to take a quick look back FreeWave has worked primarily in the industrial markets for 27 years, most notably with oil and gas, utilities, and water/wastewater. We would occasionally take on side projects with the military helping out their robotics teams with drones and other technologies, but we have traditionally focused on robust, narrowband communications links. And when I say “narrowband,” I mean the very, very small bits of data that go back and forth in SCADA systems or command and control systems in general. When I came aboard four years ago, the idea was to start pivoting FreeWave toward IIoT in the edge. We began developing radio hardware in the narrowband world that would allow us to do edge computing. As a radio company, this was trailblazing stuff, and we weren’t quite aware of what we were getting ourselves into. Now, before diving deeper, I’d like to reflect on last year’s events. A Look Back at 2020 The pandemic caused us to make significant changes. FreeWave started 2020 with many legacy products and product lines, and it became hard to find the components we needed to push those products forward. We recognized that we’d need to do a significant uplift of these legacy products by rebuilding them from the ground up and ensuring that they were backward-compatible with everything else we had out in the marketplace. After all, we were still talking about 900 megahertz products! In July, we acquired a small software company with a robust solution set focused on proprietary protocols. The acquisition allowed us to focus on the edge with a whole other engineering team section, which is fantastic. Because of this acquisition, our edge computers now come native with protocol converters, which means you can translate proprietary languages brought into the cloud into any language you want. In my opinion, our transition from a primarily OEM and widget manufacturer into a full-blown software application company was a massive win. On top of that, we are currently updating a full SCADA suite that’s been well-received. What You Can Expect from FreeWave in the Next 12 Months We are excited about our 2021 product roadmap as we make a significant leap forward into Edge Computing. This quarter, we will be releasing two new products: FreeWave Edge and FreeWave Fusion Bridge. FreeWave Edge is a data platform that lets customers extract real-time information from their sensors and devices. Edge also allows users to customize alerts and data processing and connects to a customer’s preferred cloud or reporting system. Edge helps companies suffering from unreliable data (or no data at all) improve their operations and, ultimately, accelerates business outcomes. Fusion Bridge is a dual-radio WiFi bridge that introduces connectivity and sensor fusion to 900Mhz networks. New FreeWave customers often have trouble accessing on-site data and quickly transmitting the information to the home office. They’ll install on-site routers to get WiFi connectivity, which can be expensive, and the equipment is usually in the open, where it’s vulnerable to theft. Fusion Bridge enables mobile equipment with WiFi to seamlessly connect smart devices with headquarters. The tool eliminates security vulnerabilities specific to an always-on remote AP and protects on-site assets through the quick and straightforward integration of off-the-shelf wireless security equipment. The Roles IIoT and Data Collection Will Play in the Future of Industrial Automation The future roles of IIoT and data collection are significant. There have been many tire-kickers on the manufacturing side, but nothing comes close to what will occur in the next few years with the various applications coming on-board. We’re entering an exciting era. FreeWave is looking at the possibility of developing – and investing in – the different ways people handle data at the edge and how people make decisions using artificial intelligence. I think this is where many companies will focus their energy — on more of the indoor IoT market, or perhaps even with things like your thermostat. All of the stuff you interact with daily. The possibilities will be endless. Critical Advancements in Data Collection and Communication Companies increasingly want to get more real-time information and insights from their data. Folks have been able to collect a limited amount of data for at least 50 years. Still, if they needed more information, they would have to send someone out to collect data in-person and report back with their findings. In an agile and increasingly competitive world, this kind of data collection is unacceptable. People want to quickly identify urgent issues on-site and make the necessary adjustments right then and there. And with today’s technological advancements, we can do just that! For example, an HR team came to us with concerns that their workers might not be wearing helmets while on a project. They needed to ensure OSHA compliance on a remote site. Using artificial intelligence on a Well Pad, we collected and reported data to them in real-time. Why Customers Return to FreeWave for Multiple Projects We offer an exceptional product; that’s why people return to FreeWave again and again. I still hear from people calling about our first product (DGR). It’s over 20 years old and still in-use! Let’s face it; when people find a reliable, durable product that works, they will continue to come back. Our exceptional customer service is another reason customers return. We provide in-house tech support in the Boulder, Colorado, area (where we also manufacture FreeWave products), and we have a 24-hour hotline for folks needing troubleshooting and installation help. Advice to Customers Customers need to question the viability of the companies with which they
FreeWave CEO Provides Valuable IIoT and Edge Computing Insights on the Talking Industrial Automation Podcast
What Does the Future Hold for IIoT, Automation, and Edge Computing? FreeWave’s CEO chats with Talking Industrial Automation Podcast to provide valuable insight on IIoT and edge computing. Talking Industrial Automation podcast host, Lisa Richter recently sat down with FreeWave CEO Kirk Byles for a timely and informative discussion on the state of industrial automation, edge computing, IIoT, and FreeWave. Here are some key points you’ll take away from the podcast. How FreeWave has transitioned from a smaller, robust narrowband communications company to an IIoT and Edge Solutions company How FreeWave has grown over the past year and what you can expect in the next 12 months The roles IIoT and data collection will play in the future of Industrial Automation Critical advancements in data collection and communication Why customers return to FreeWave for multiple projects And lots more. You can listen to the entire podcast here!