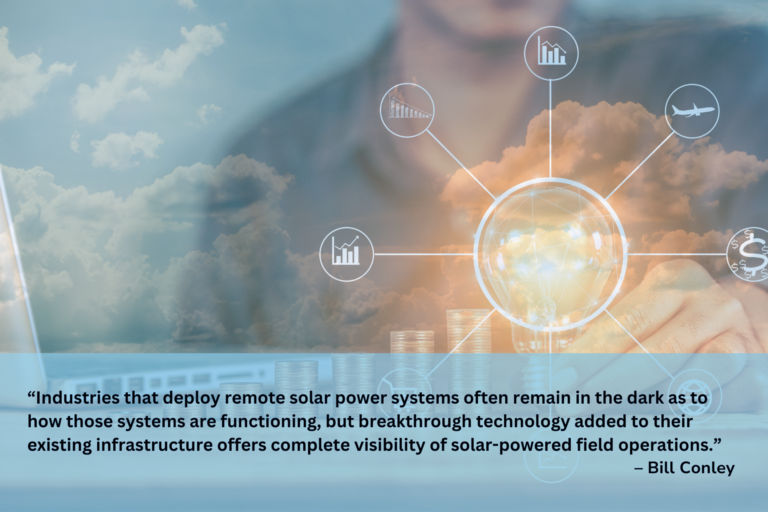
It’s not easy to write about solar energy without getting carried away with metaphors. In a world facing a worsening climate crisis, solar power — as a renewable energy source — represents a ray of hope, a bright spot, a beacon of light. Solar power’s day in the sun has been a long time coming. Before he died in 1931, inventor Thomas Edison reportedly told friends, “We are like tenant farmers, chopping down the fence around our house for fuel, when we should be using nature’s inexhaustible sources of energy — sun, wind, and tide. … I’d put my money on the sun and solar energy. What a source of power!”
Today, many diverse industries are putting their money on solar power. But, in many cases, it’s not a sense of urgency about “going green” that drives them. In industries operating in farflung, remote locations, the use of solar power is usually driven by pure necessity — there’s simply no other viable power source. While there’s excitement around the promise of solar energy, my conversations with industry leaders often center on the problems associated with remote solar power systems, including a lack of visibility around solar-powered battery performance. Since battery failure can cause safety hazards and even halt production, operators take extreme — and expensive — measures to prevent it.
Our customers’ pain points led to the development of a breakthrough, all-in-one-box solution that can be easily added to existing infrastructure to slash maintenance costs and reduce risk factors by providing critical data on remote solar power system performance.
I invented this technology, but before I tell you all about my “baby,” let’s look more closely at the pain points it helps to address and the cost savings and other benefits it provides.
Eliminating the Guesswork Around Solar-powered Battery Performance
While solar-powered devices reliably monitor field operations as a whole, a lack of visibility around the performance of the solar-powered batteries themselves is a huge blind spot and cost driver.
Oil and Gas (O&G), wastewater management, and utilities are among the major industries that rely on solar power, principally to operate remote sensors and devices that send critical information back to a centrally located SCADA system. This data tells the SCADA operator what’s going on in the field.
For example, O&G personnel are alerted if equipment goes down or if various pressures and temperatures reach unsafe levels. Powering the devices that relay this information depends on reliable battery performance, which, in turn, depends on the availability of sunlight to power the batteries.
Touting the pros of solar power, Elon Musk famously said the sun “shows up every day” and “just works.” In reality, the sun doesn’t always shine sufficiently to fully charge solar batteries, and, as we all know, it clocks out every night without fail. So, operators have tried to optimize battery performance by doing calculations to determine the amount of current needed to power the devices, including an estimate of autonomy time — the number of days that a battery charge will last should the solar panels stop absorbing sunlight. While these calculations initially suggest which sizes and configurations of solar panel and battery systems are needed to produce the required current, they don’t take into account equipment deterioration over time or the power requirements of any equipment added down the line.
Hours of autonomy, so painstakingly calculated in what amounts to a paper exercise, are also affected by extreme ambient temperatures and other conditions. To avoid power disruptions and production downtime, O&G producers have taken to replacing all of the batteries every six months, regardless of need or individual battery performance. It’s not uncommon for a major producer to have several thousand remote, solar-powered sites, so battery storage and replacement are substantial budget items. One major producer mentioned they spend $1.4 million annually — just on batteries.
Callouts and lockups are also expensive — and less predictable. A callout occurs when a system goes offline and stops sending SCADA communications, triggering a truck roll to the site to determine the cause. Equipment lockups require technicians to drive to the site to power-cycle the affected assets no matter where that site is, all for a process that takes 20 seconds to perform, sandwiched between hours of drive time.
Considering that each and every truck roll costs as much as $2,400, eliminating set-schedule battery replacements, manual power cycling, and most service calls could easily save millions of dollars.
So, let’s talk about the solution.
Introducing Solar Site Analytics
Having collaborated with customers to understand the problems and limitations they were experiencing with solar-powered operations, we developed a patent-pending solution that provides complete visibility of solar-powered field operations, along with other essential features. Contained in one compact box, the product packs smart monitoring and analytics capabilities that prevent production losses, reduce labor costs, improve worker safety, and predict power system degradation or failure, including:
- Accurate hours-of-autonomy calculations in real time
- Real-time updates on battery and solar panel sizing requirements for maximum efficiency
- Battery capacity levels, which indicate when a battery actually needs to be replaced
- Automatic power cycling in the event of a lockup
- Analytics that detect anomalies and predict maintenance needs before solar power system components go down
- Automatic load shedding and load prioritization to protect batteries from excess voltage
- As an added feature, it also includes a maximum power point tracking (MPPT) charge controller — the most efficient controller for industrial solar power system applications
The product can connect to a customer’s existing SCADA system or connect directly to the FreeWave cloud-based data analytics platform. With it, operators can monitor temperatures, pressures, and other metrics, along with battery and solar panel status and performance — from capacity levels and days of autonomy to predictive maintenance forecasts.
FreeWave’s patent-pending remote solar power system manager has been in development for years and, in nearly a decade of field testing, not one instance of critical failure to monitored system components has been reported. And, the monitor offers a swift return on investment, paying for itself as soon as its intelligence supplants one single site visit for maintenance and troubleshooting. We’re excited to bring this to market and help our customers increase efficiencies across off-grid installations.
Stay tuned for upcoming blogs where we’ll share some real-life use cases we’re seeing for this solution. In the meantime, we’re inviting new and existing customers to join our growing alliance of beta users as we continue to evolve the product to exceed your needs. To learn more about this opportunity and experience firsthand how FreeWave’s breakthrough technology can shed light on your remote solar-powered operations, contact us about signing on as a beta user.